Cosa sono i tailored blanks
Chiamati anche Tailor Welded Blanks (TWB), sono pannelli di lamiera composti da elementi di materiali e/o spessori differenti saldati insieme. Tipicamente destinati allo stampaggio, uniscono acciai di differente resistenza per ottenere parti con caratteristiche specifiche a seconda della zona. L’applicazione più comune è nel settore dell’auto. Vengono usati per creare profili con zone in grado di resistere alle deformazioni e zone deformabili per assorbire l’energia dell’impatto, oppure per rinforzare i punti soggetti a carichi maggiori, come in prossimità delle cerniere delle portiere.
Le alternative ai tailored blanks
Scocca monoblocco
Prima dell’avvento dei tailored blanks, le scocche erano realizzate con una sola tipologia e spessore di acciaio, con un solo elemento per ogni parte dell’auto. Questa soluzione monolitica comporta una grande quantità di sfridi, come ad esempio nelle portiere o nei pezzi di forma molto irregolare.
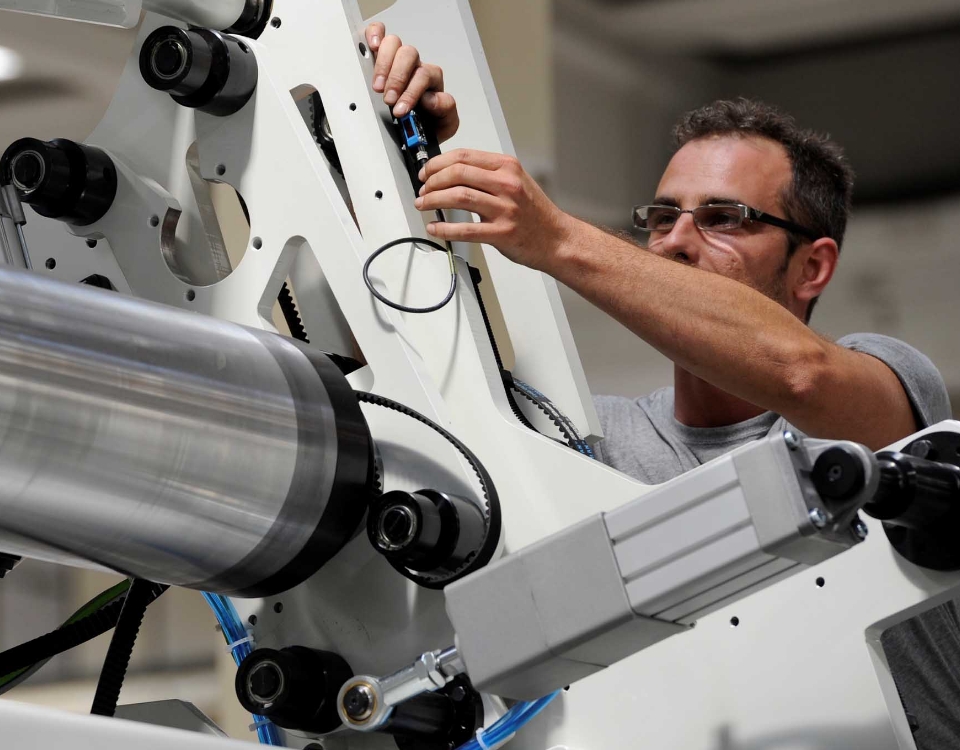
Giunzione a punti
I componenti dell’auto erano realizzati unendo tramite saldatura a punti lamiere di forma ottimizzata per la riduzione dello sfrido. Il metallo utilizzato non aveva caratteristiche differenti a seconda della funzione richiesta.
Questa soluzione, pur rappresentando un passo avanti, porta con sè una serie di svantaggi:
• lembi sovrapposti
I due fogli devono essere giuntati a lembi sovrapposti, con un aumento di peso e di spessore.
• corrosione
La giunzione diventa un punto dove possono infiltrarsi umidità e polvere, con il rischio di corrosione. Va quindi sigillata, nei punti più esposti, tramite cordoni di saldatura, che fanno aumentare i tempi e i costi di produzione.
<
• aumento di peso
Per rinforzare le zone soggette a carichi maggiori, l’unica soluzione era utilizzare fogli più spessi, oppure aggiungere localmente dei rinforzi.
Successivamente, con l’adozione degli acciai speciali, si sono potute ottenere zone a resistenza differenziata. Le parti soggette a sforzi maggiori venivano realizzate con acciaio altoresistenziale, ma la saldatura era ancora per punti. Rimanevano quindi i problemi dei lembi sovrapposti e del rischio di corrosione.
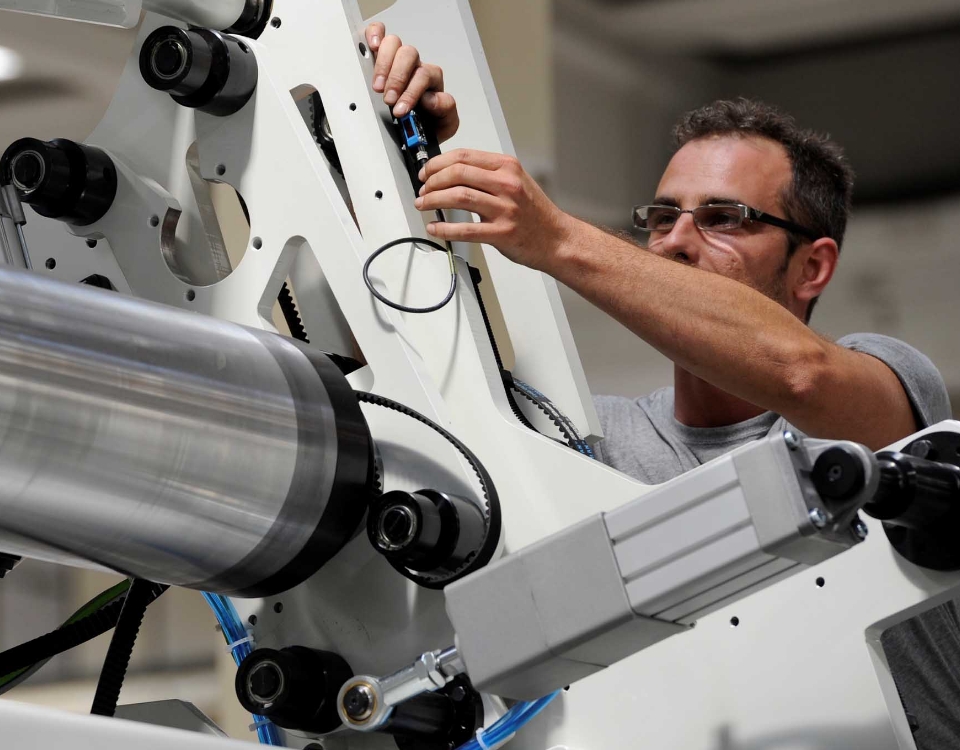
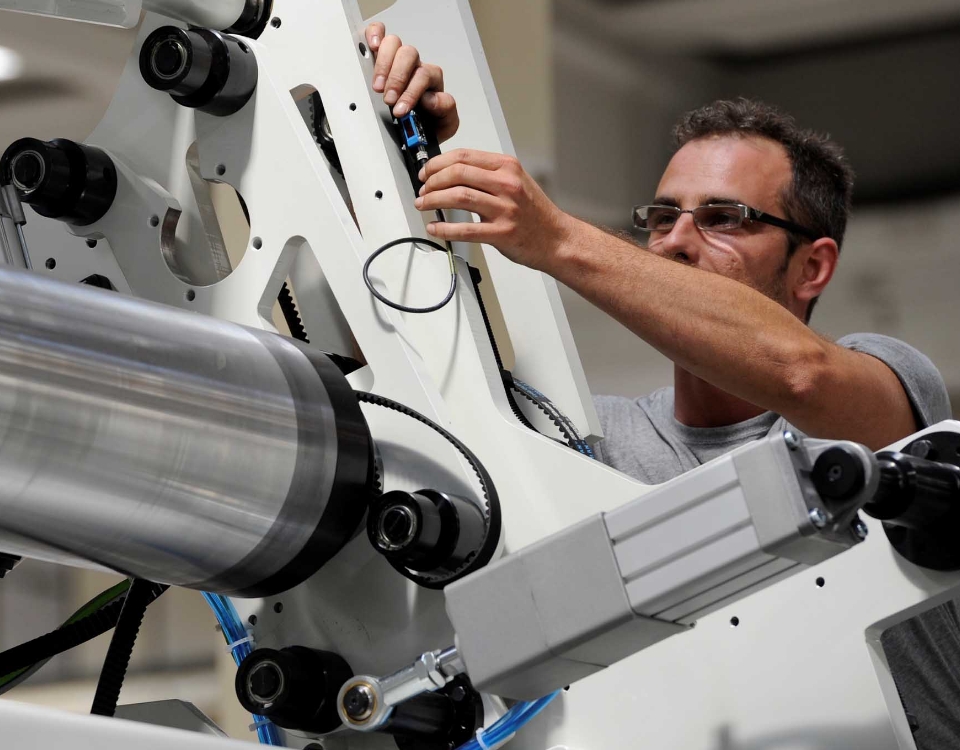
Il cambiamento maggiore è arrivato con l’utilizzo di lamiere saldate testa-testa tramite laser, che ha finalmente permesso l’uso di acciai diversificati senza gli inconvenienti della saldatura a punti.
I vantaggi principali nell’uso di tailored blanks sono:
- riduzione degli sfridi
possiamo utilizzare nesting ottimizzati per le varie forme, riducendo il materiale sprecato. Di conseguenza si riducono i costi di acquisto, di stoccaggio, di manipolazione e di smaltimento.
- aumento della sicurezza
Utilizzando acciai altoresistenziali possiamo creare cellule di sicurezza e zone di deformazione che assorbono l’energia dell’impatto.
- riduzione del peso
Gli acciai altoresistenziali garantiscono le stesse prestazioni degli acciai comuni ma con un minore spessore. Possiamo ridurre il peso della vettura, aumentando l’efficienza e diminuendo i consumi di carburante. La saldatura laser testa-testa inoltre elimina la sovrapposizione del materiale e di conseguenza il peso aggiuntivo.
- riduzione della corrosione
eliminando la fessura tra una lamiera e l’altra, tipica della saldatura a punti, non creiamo una zona potenzialmente attaccabile dalla ruggine.
- efficienza produttiva
utilizzare tailored blanks in altoresistenzale saldati a laser consente di ridurre il numero di saldature e lavorazioni da effettuare in-house oppure di accorparle, riducendo i costi e i tempi di produzione. Ad esempio, con la lavorazione tradizionale è necessario tranciare e stampare separatamente sia il pannello portiera che il rinforzo cerniere, e poi unirli. Con i Tailor welded blanks, i due fogli sono prima saldati e poi stampati, eliminando uno stampaggio.
- migliore precisione
Diminuire il numero di lavorazioni come stampaggio ed assemblaggio permette di controllare con accuratezza le dimensioni dei vari componenti e del pezzo finito, riducendo la necessità di successive lavorazioni.
- migliore finitura
La saldatura testa-testa è esteticamente meno visibile e può essere comunque nascosta più facilmente rispetto alla giunzione a lembi sovrapposti.
- minori costi di gestione
I Tailor welded blanks consentono di ridurre sia lo spazio occupato a magazzino che il numero totale di codici da gestire, diminuendo i costi logistici ed amministrativi
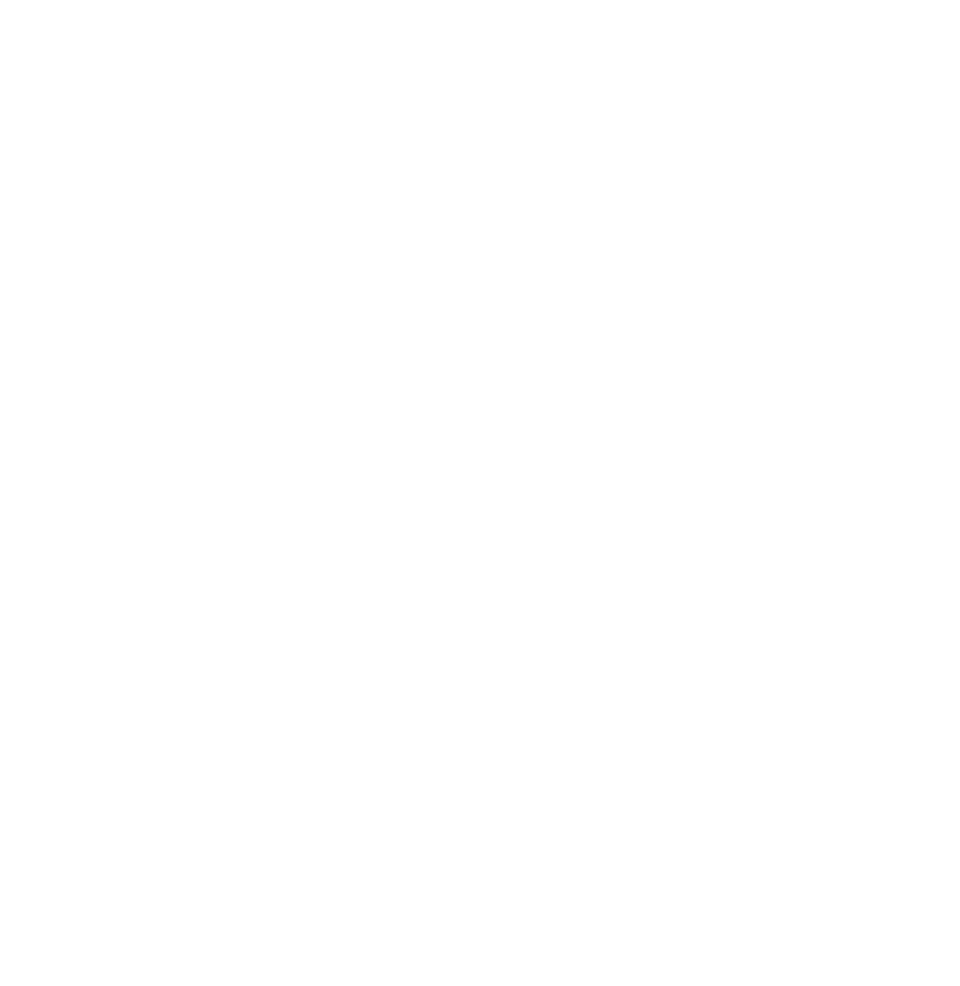
Ovviamente anche l’approccio Tailored Blanks comporta degli aspetti negativi:
- costo del blank
Realizzare i tailored blanks comporta un costo iniziale maggiore, che però viene compensato dai vantaggi portati all’utilizzatore finale, come maggiore sicurezza e riduzione dei consumi.
- maggiore costo dei macchinari
I tailored blanks richiedono strettissime tolleranze dimensionali e un’elevata qualità nella saldatura per sopportare le lavorazioni di stampaggio e per garantire la sicurezza dei passeggeri. Per ottenere queste prestazioni è fondamentale l’utilizzo di macchinari molto precisi.
Esigenze produttive
- taglio a freddo
Gli acciai da stampaggio sono rivestiti con leghe metalliche a basso coefficiente di attrito. È importante che questi elementi non inquinino lo spessore della lamiera, andando ad alterare le caratteristiche del metallo. Questo si verifica con il taglio termico, perciò la cesoiatura o la tranciatura sono preferibili. La contaminazione della saldatura è realmente il motivo primario per cui si utilizza un taglio meccanico, rinunciando alla flessibilità del laser o del plasma. In questo tipo di prodotti, dove le lamiere vengono saldate testa-testa, è fondamentale che la zona saldata sia resistente come il metallo base, senza inclusioni che la andrebbero ad indebolire fortemente.
- processo di taglio
Alcuni tailored blanks prevedono l’uso di acciai speciali UHSS, con durezza anche fino a 1500 MPa: 5 volte più del normale acciaio da costruzione. Con questi acciai così resistenti, la cesoiatura raggiunge il limite fisico del processo: invece di tagliarsi, il metallo rischia di fessurarsi. Si possono verificare cricche che si propagano anche perpendicolarmente alla linea di taglio, seguendo le fibre della lamiera.
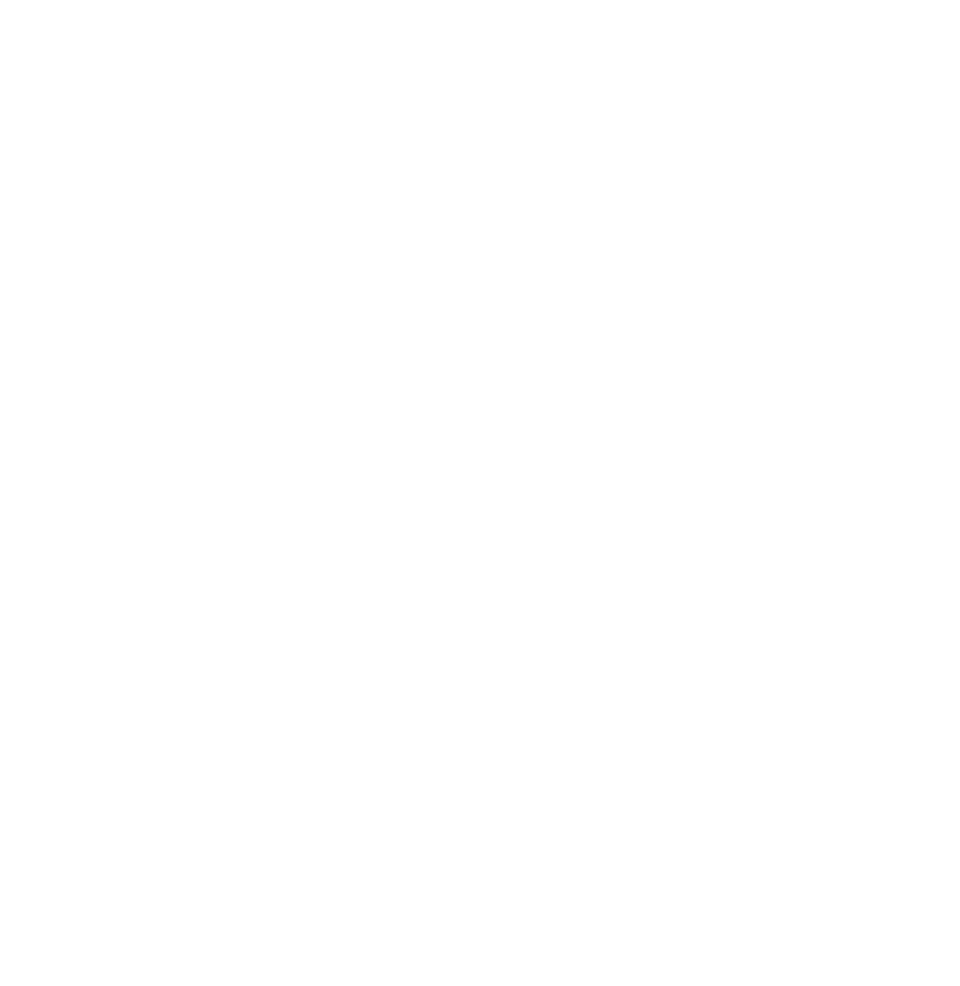
- rettilineità
La saldatura a laser deve essere totalmente priva di difetti, per sopportare il processo di formatura e resistere agli impatti senza cedimenti. Per questo motivo la tolleranza sulla rettilineità del taglio è molto stretta. È fondamentale utilizzare cesoie strutturalmente molto solide e in grado di garantire un taglio perfetto anche con i materiali più resistenti. Le cesoie X-Cut Gasparini, dotate del sistema Blade Pads, sostengono la lama ed impediscono deflessioni anche con gli sforzi più intensi. Inoltre, l’uso di premilamiera speciali realizzati appositamente per questa applicazione permette di ottenere la sezione cesoiata uniforme su tutta la lunghezza.
- saldatura laser
Gli acciai altoresistenziali devono le loro caratteristiche uniche ad una precisa miscela di elementi e a specifici trattamenti termici controllati. La saldatura laser, non utilizzando nessun materiale d’apporto, garantisce che venga mantenuta la composizione chimica originale. Grazie all’estrema focalizzazione del raggio, anche la zona termicamente alterata viene ridotta al minimo.
Fonte
Photo credit:
- BMW Werk Leipzig
- Gasparini Industries – own work