What are tailored blanks?
Also called Tailor Welded Blanks, they are sheet metal panels made of elements of different materials and/or thicknesses welded together. Typically intended for stamping, they combine steels of different strengths to obtain parts with specific characteristics depending on the area. The most common application is in the automotive industry. They are used to create profiles with zones capable of resisting deformation and deformable zones to absorb the energy of the impact, or to reinforce points subject to higher loads, such as near the hinges of the doors.
Alternatives to tailored blanks
Monocoque
Before the advent of tailored blanks, chassis were made of only one type and thickness of steel, with only one element for each part of the car. This monolithic solution involves a large amount of scrap, such as in doors or very irregularly shaped parts.
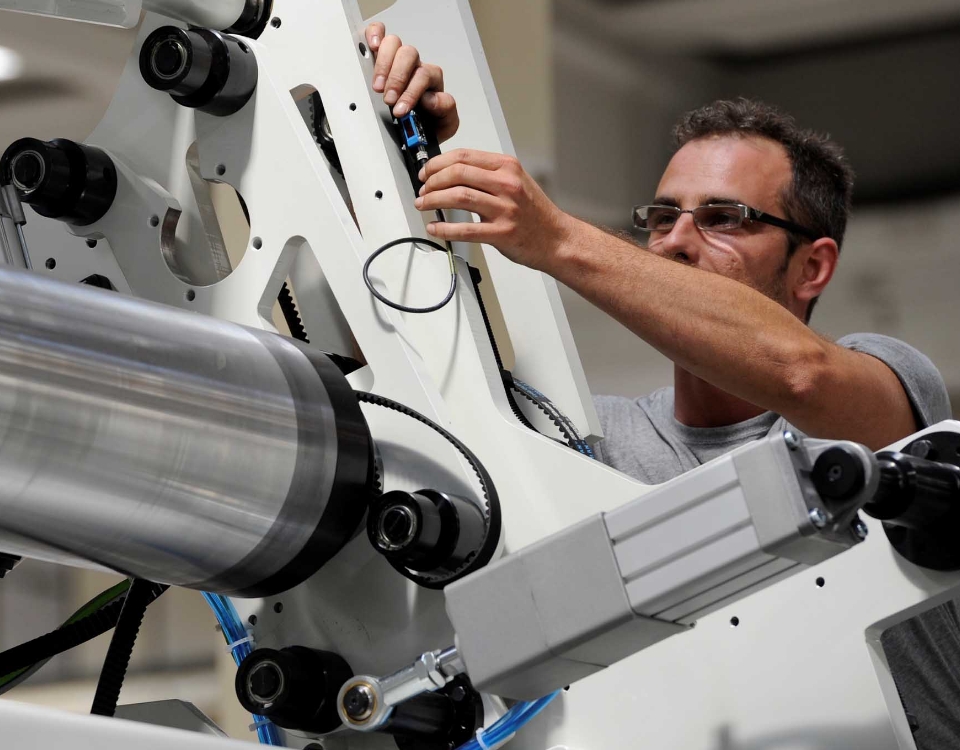
Spot welding
The car components were made by joining by spot welding sheets of optimized shape for the reduction of scrap. The metal used did not have different characteristics depending on the function required.
This solution, while representing a step forward, brings with it a number of disadvantages:
• overlapping edges
The two sheets must be joined with overlapping borders, with an increase in weight and thickness.
• corrosion
The joint becomes a point where moisture and dust can infiltrate, with the risk of corrosion. It must therefore be sealed at the most exposed points by means of welding seams, which increase production times and costs.
• weight increase
To reinforce areas subject to higher loads, the only solution was to use thicker sheets, or add stiffeners locally.
Subsequently, with the adoption of special steels, it was possible to obtain zones with differential resistance. The parts subject to the greatest stress were made of high-strength steel, but the welding was still spot welding. The problems of overlapping edges and the risk of corrosion remained.
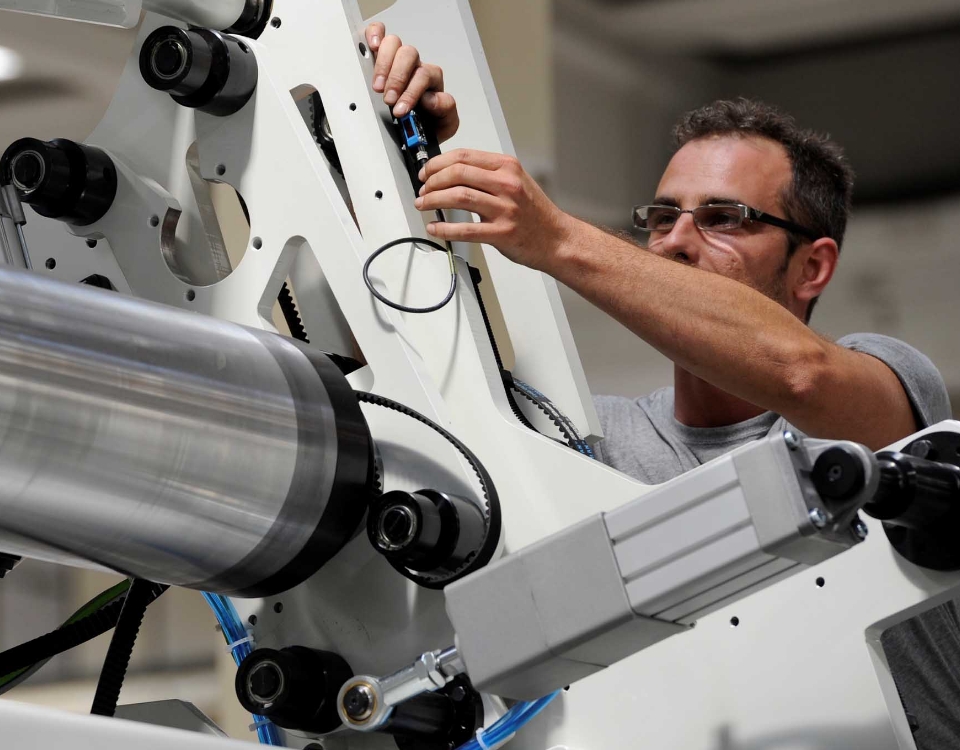
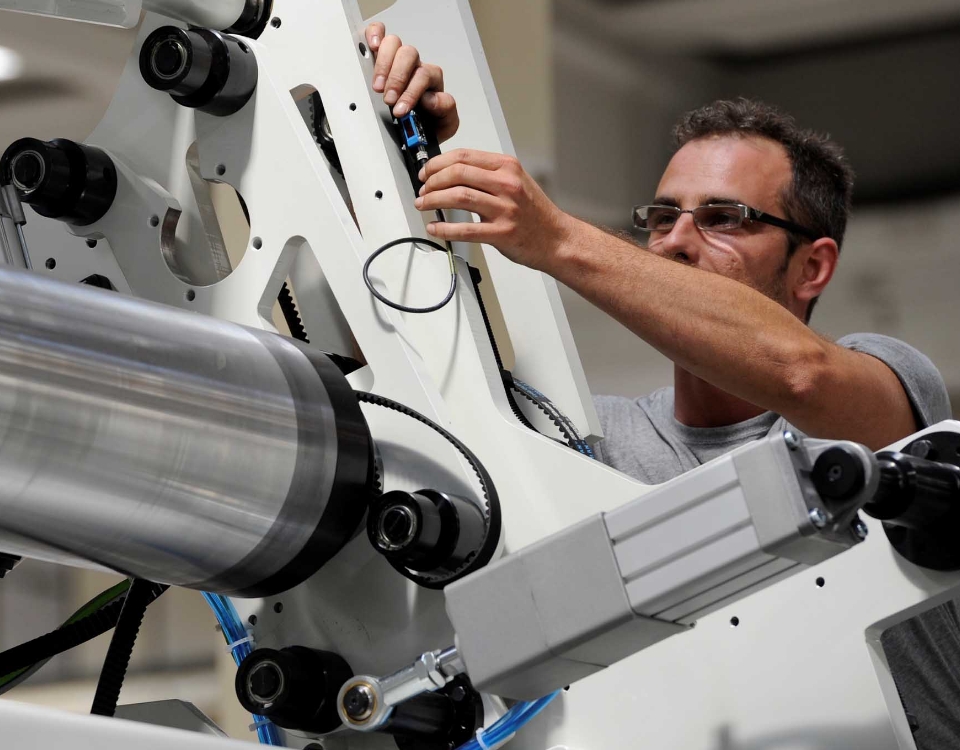
The biggest breakthrough came with the use of butt-joint laser-welded sheet metal, which finally allowed the use of diversified steels without the drawbacks of spot welding.
The main advantages in the use of tailored blanks are:
- scrap reduction
we can use nesting optimized for various shapes, reducing the material wasted. As a result, the costs of purchasing, storage, handling, and disposal are reduced.
- increased safety
By using high-strength steels we can create safety cells and crumple zones that absorb the energy of the impact.
- weight reduction
High strength steels provide the same performance as common steels but with a lower thickness. We can reduce the weight of the car, increasing efficiency and reducing fuel consumption. Laser butt-joint welding also eliminates material overlap and therefore additional weight.
- corrosion reduction
By eliminating the interstice between the sheets, typical of spot welding, we do not create an area that could potentially be attacked by rust.
- production efficiency
Using laser-welded high-strength tailored blanks reduces the number of welds and processes to be carried out in-house, or enables them to be combined, reducing production costs and time. For example, with traditional processing, both the door panel and the hinge reinforcement need to be punched and stamped separately, and then joined together. With Tailor welded blanks, the two sheets are first welded and then stamped, eliminating one stamping operation.
- better accuracy
Reducing the number of processes such as stamping and assembly allows to accurately control the dimensions of the various components and the finished part, reducing the need for subsequent processing.
- better finish
Butt-joint weld is less visually noticeable and can still be hidden more easily than the overlapping edge joint.
- lower operating costs
Tailor welded blanks reduce both the space occupied in the warehouse and the total number of codes to be managed, reducing logistical and administrative costs.
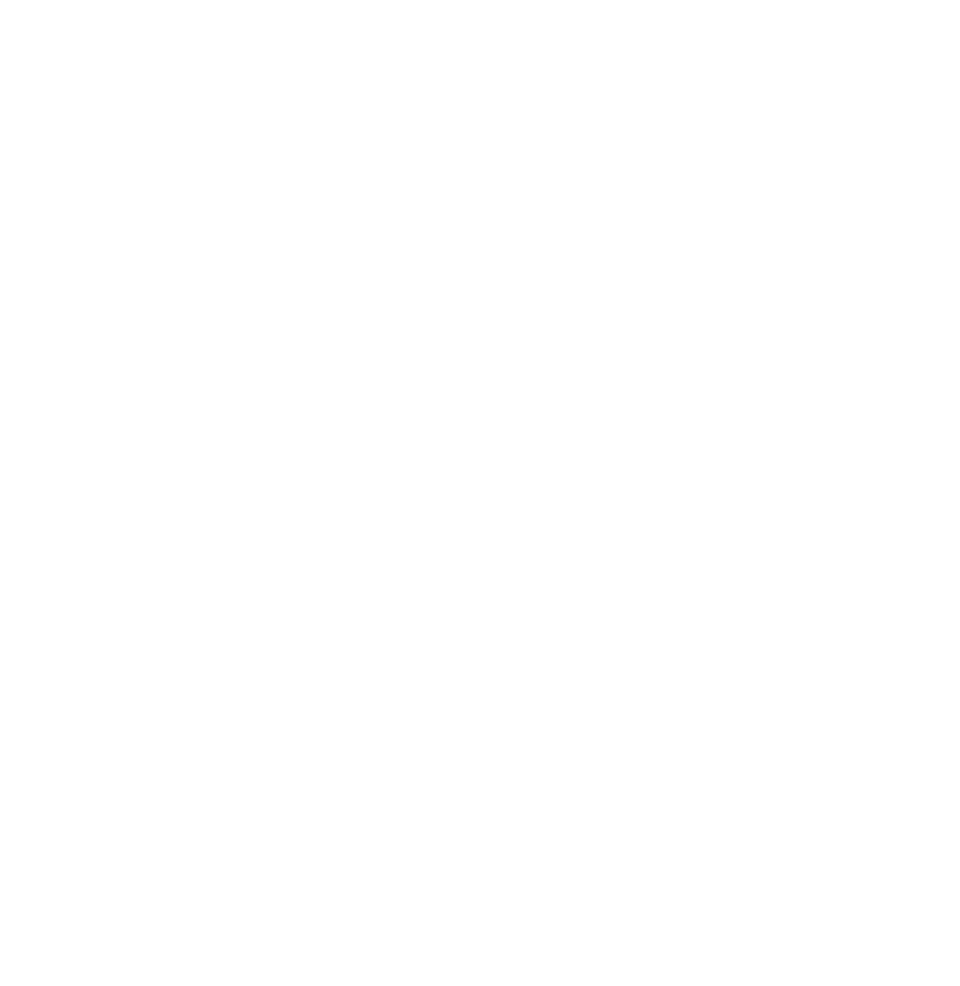
Of course, the Tailored Blanks approach also has its drawbacks:
- cost of the blank
Making tailored blanks involves a higher initial cost, but this is compensated by the advantages brought to the end user, such as greater safety and reduced fuel consumption.
- higher cost of machinery
Tailored blanks require very tight dimensional tolerances and high welding quality to withstand stamping operations and to ensure passenger safety. To achieve this performance is essential to use very precise machinery.
Production requirements
- cold cutting
Stamping steels are coated with low-friction metal alloys. It is important that these elements do not pollute the thickness of the sheet metal, altering the characteristics of the metal. This is the case with thermal cutting, so shearing or blanking are preferable. Contamination of the weld is really the primary reason why mechanical cutting is used, sacrificing the flexibility of laser or plasma cutting. In this type of product, where the sheets are butt-joint welded, it is essential that the welded area is as strong as the base metal, without inclusions that would weaken it significantly.
- cutting process
Some tailored blanks require the use of special UHSS steels, with hardness up to 1500 MPa: 5 times more than common construction steel. With such a high strength steel, shearing reaches the physical limit of the process: instead of cutting, the metal may crack. There may be cracks that propagate even perpendicularly to the cutting line, following the fibers of the sheet metal.
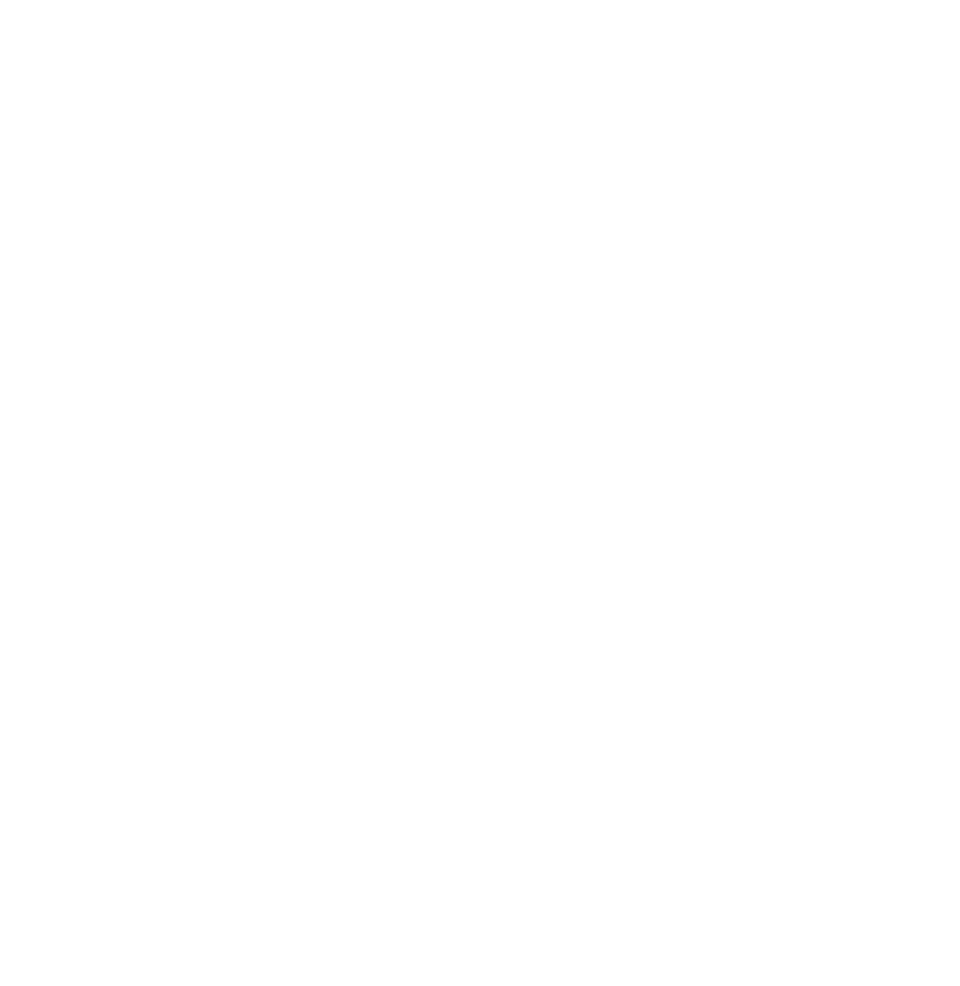
- straightness
Laser welding must be completely free of defects, to withstand the stamping process and withstand impact without failure. For this reason the tolerance on the straightness of the cut is very narrow. It is essential to use shears that are structurally very stiff and able to guarantee a perfect cut even with the most resistant materials. Gasparini X-Cut shears, equipped with the Blade Pads system, support the blade and prevent deflections even with the most intense efforts. In addition, the use of special blank hold-down cylinders made specifically for this application makes it possible to obtain a uniform sheared section over the entire length.
- laser welding
High strength steels owe their unique characteristics to a precise mixture of elements and specific controlled heat treatments. Laser welding, using no filler material, ensures that the original chemical composition is maintained. Thanks to the extreme focus of the beam, even the heat affected zone is reduced to a minimum.