What it means to choose a fully customised press brake
The machine has been set up with the SuperCustom configuration: it is completely made to measure in open height, stroke, throat, and tool adapters height.
This press brake is designed with:
- E-Reflex deformation compensation system, which ensures the control of the structure’s deflections through a network of sensors, located both inside the machine and in the hydraulic system;
- Gasparini adaptive crowning system, which, using two precision sensors, detects the deformation of the upper ram and drives the lower beam accordingly.
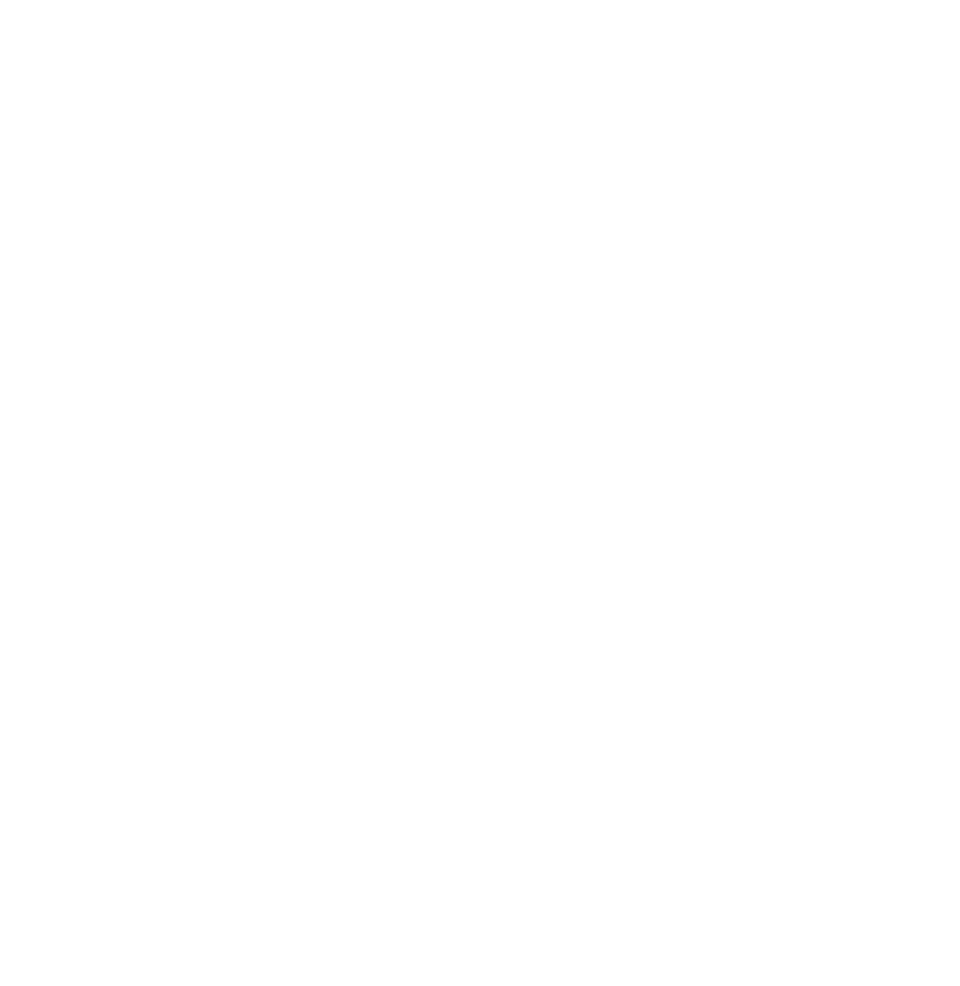
The choice of pneumatic clamping system
With regard to clamping, the customer opted for:
- Gasparini AirSlide upper pneumatic clamping of 900 mm height for European type tools
- crossbar clamping with sliding rollers
- self-aligning hydraulic clamping for tool adapters height over 400 mm
- manual lower clamping
In particular, based on the Irinox requirement, the crossbar clamping system with sliding rollers was implemented. In this way it is possible to move the tool adapters easily, without any effort on the part of the operator, as the weight is supported by the system itself. This type of clamping also allows them to be moved to external positions for the passage of boxes.
Choosing the CNC
In selecting the CNC, the customer opted for the Delem DA-69T, whose user interface allows fast collaboration between programming and production, and which also allows 3D programming. For offline software, the Delem Profile-T 3D was selected, which in addition to enabling the aforementioned programming, allows the import of DXF, STP and IGES format files. In addition, communication standards compliant with Industry 4.0 Intelligent Factory models were installed, and the Tele-Link remote assistance function was set up.
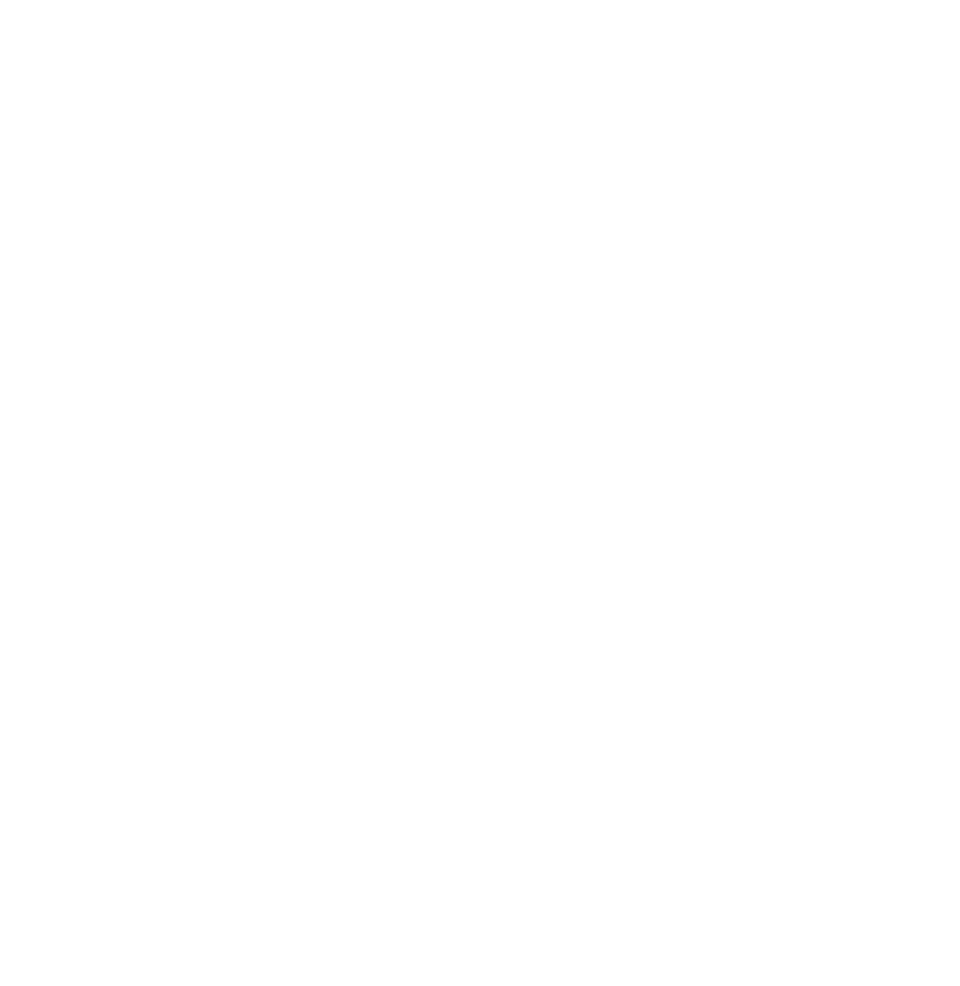
The safety device is the DSP-AP Laser, which provides a reduction in speed and a decrease in cycle time. The system emits a visible laser beam that meets EN12622 standards, ensuring the operator is protected from any danger of crushing between the die and the punch.
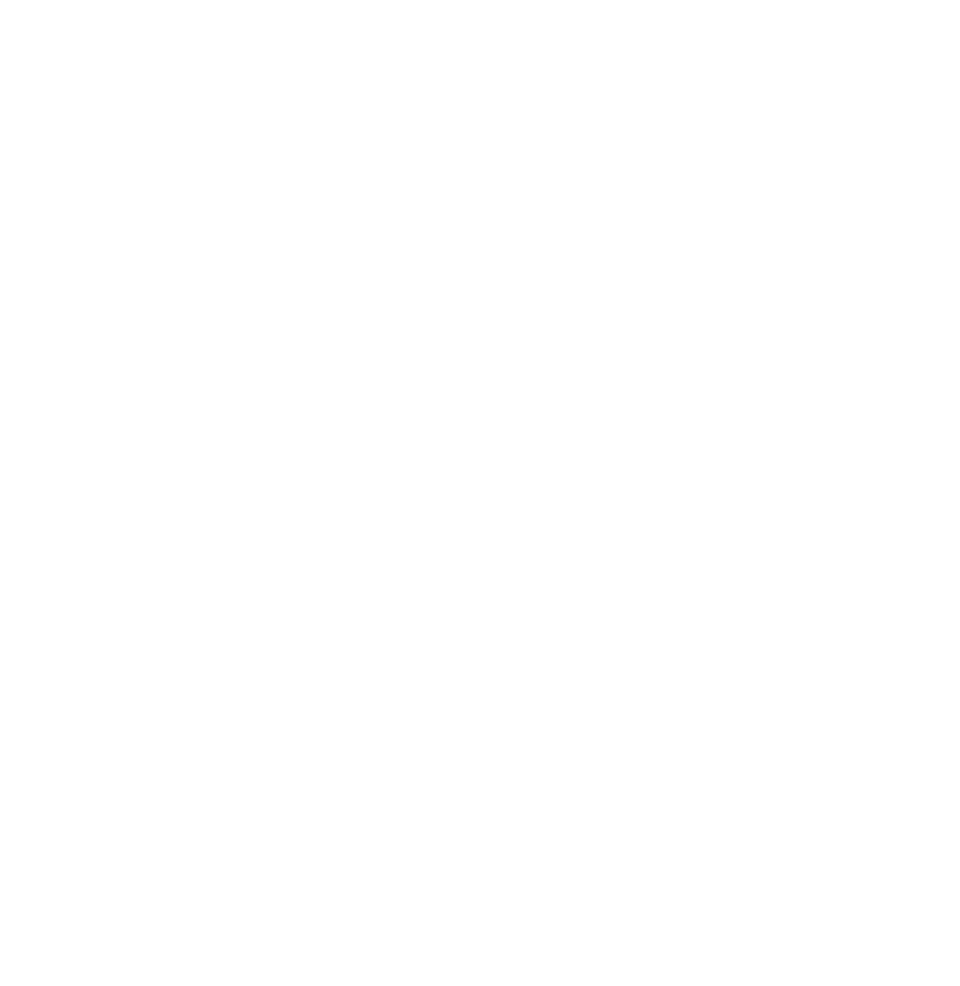
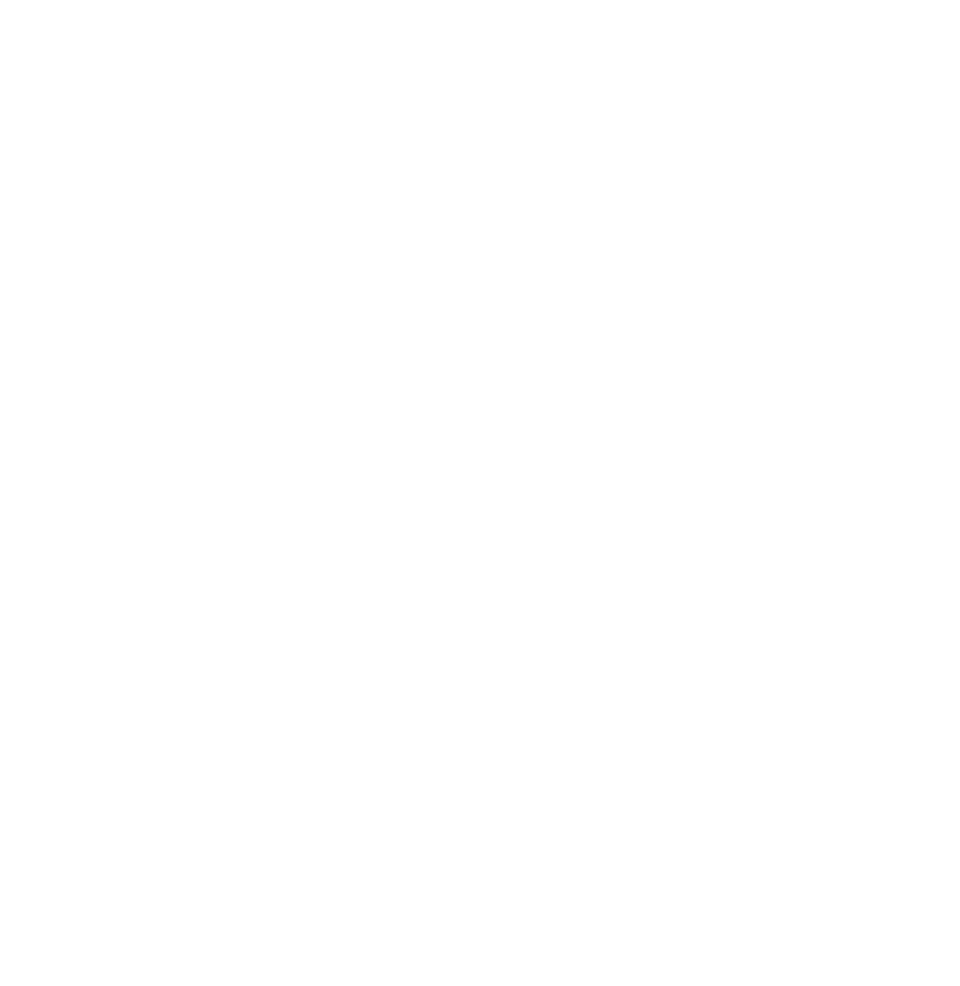
Sheet lifters and footpedals
This press brake has several foot pedals:
- a standard foot pedal (i.e. wired)
- a support pedal for the second operator
- a wireless sliding foot pedal
- a low foot pedal with only pedals
The addition of two sheet lifters with manual adjustment of the R-axis was planned. These are mobile sheet metal supports placed at the front of the machine, at the height of the bending line, controlled by the CNC. They help support the sheet metal during the bending process.