But what is Industry 4.0 and how do these concepts apply in sheet metal bending? The aim of Industry 4.0 is to make complexity increasingly functional and efficient. And the first aspect concerns the collection of data, which must be analysed and interpreted to derive value from it. This leads to ‘machine learning’, i.e. machines that perfect themselves by ‘learning’, and to the new paradigm of human-machine interaction, which involves ‘touch’ interfaces and augmented reality. Finally, there is the aspect that encompasses the transition from digital to ‘real’, i.e. additive manufacturing, 3D printing, robotics, machine-to-machine interactions and new technologies for storing and utilising energy in a targeted manner, rationalising costs and optimising performance.
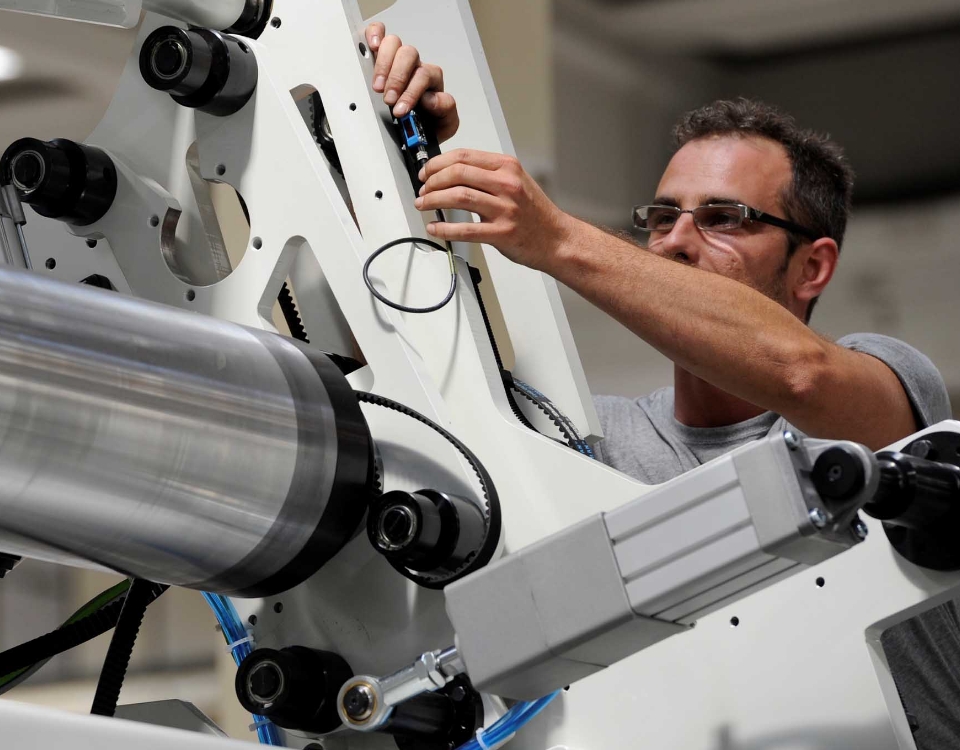
Gasparini has also been pursuing this digital transformation in a concrete way for a few years now. So much so that our press brakes have received Certification from the Pordenone Technological Pole, as they are in line with the Industry 4.0 model. The directions taken to arrive at the Intelligent Factory, also in the sheet metal sector, are those of interconnection, thanks to open and robust communication standards that allow Gasparini’s press brakes and guillotine shears to interface with other machinery and information systems, and of sensorization, or the ability, thanks to a network of sensors to detect operating parameters and send them to data collection and reporting tools, to have everything under control.
The result is a modern machine that, through CNCs, can import bending programs or technical drawings and perform advanced functions, such as monitoring press brake operation and doing remote maintenance work even remotely through the Telelink system. The data collected and managed by the software, then also offer useful information for quality control, predictive analysis, preventive maintenance, failure prevention, part tracking, job progress, processing times, material behavior and more. A technological shift that, at Gasparini, from innovation leads to value.
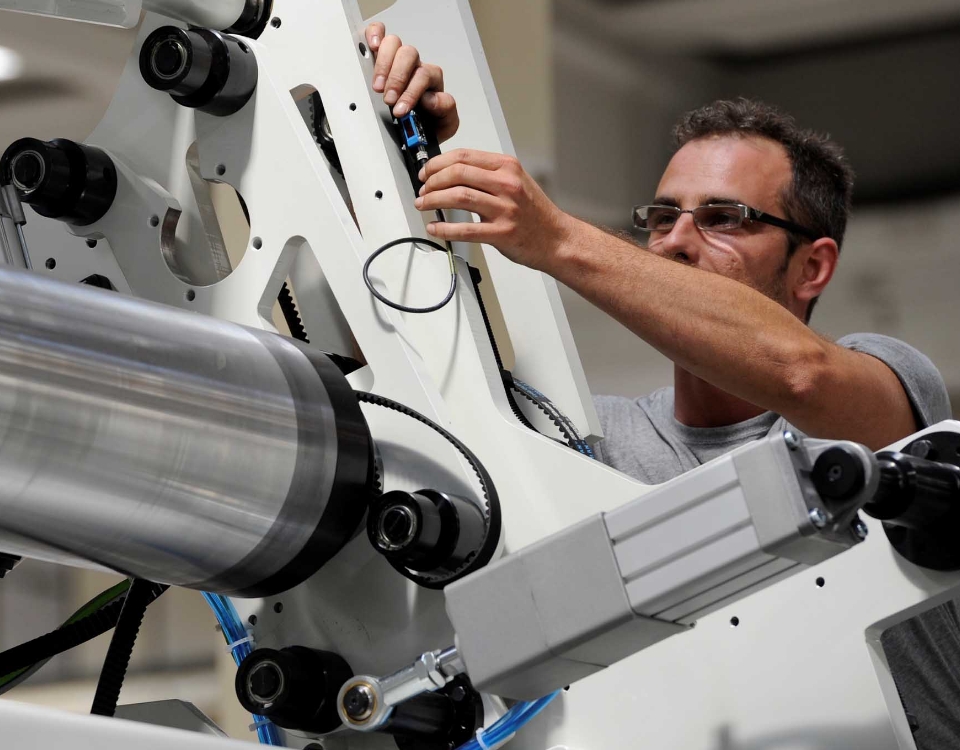