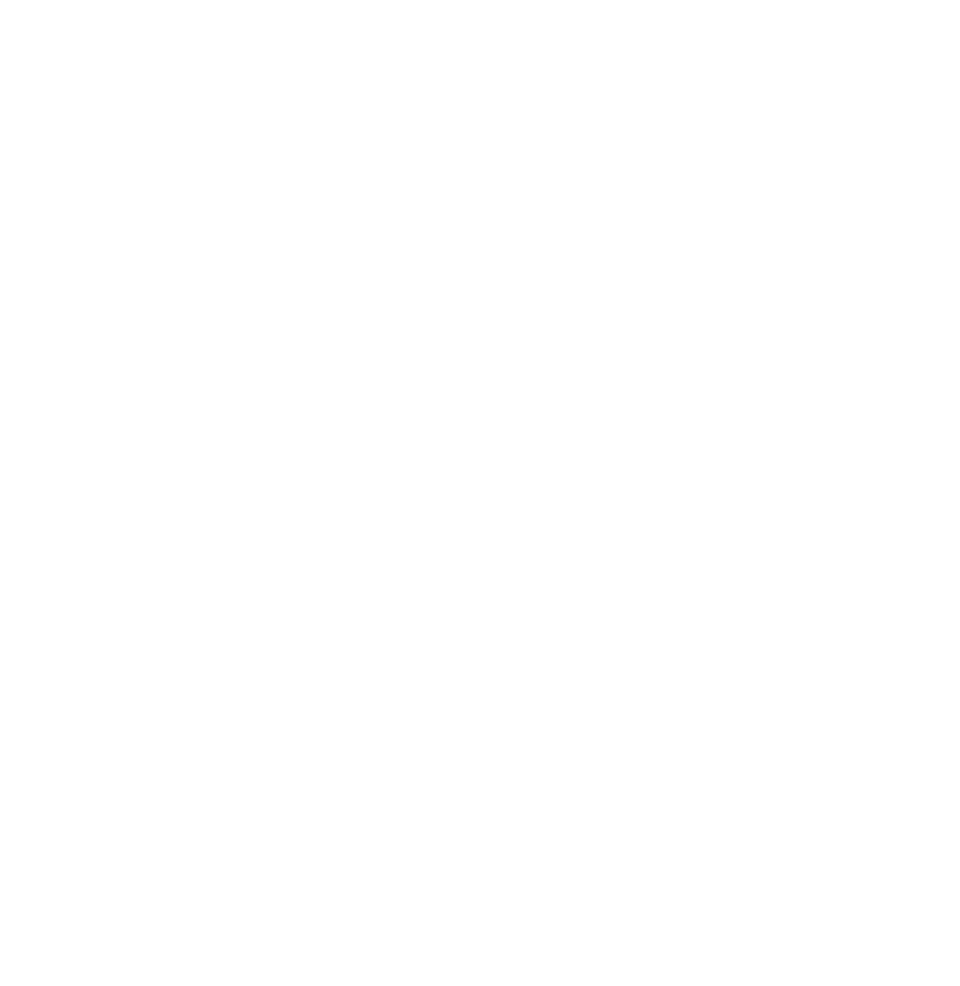
The main technical features of the press brake
The press brake is designed with our Next design. The open-height is 500 mm, and the Y-axis travel is 300 mm. In addition, the working area is equipped with LED lighting. This machine has been implemented with the Tele-Link remote service function and its Delem CNC technology is DA-66T, while the offline software is Delem Profile Lite TL 2D.
The machine is equipped with the E-Reflex deformation compensation system, which monitors the bending of the structure through a network of sensors located both inside the machine and in the hydraulic system. These sensors detect any anomalies and compare the position of the beam with the oil pressure to determine the actual position of the punch, regardless of deformations. The E-Reflex system on this bending machine works in conjunction with the automatic hydraulic bending system.
Precision and versatility of the press during bending: how we achieved it
The backgauge is four-axis (X-R-Z1-Z2) CNC-controlled, which in addition to the two standard axes also features the Z1 and Z2 axes. In addition, two additional manually manoeuvrable references (mounted on linear guides) have been added. This allows greater adaptability of the machine to the types of parts to be machined. The rear references incorporate an anti-collision safety device that releases them in the event of violent impacts to prevent damage or displacement from their correct position, allowing the operator to easily reposition them. The Z1-Z2 axes allow lateral movement of the references to simplify the positioning of parts of different lengths or to work on several stations.
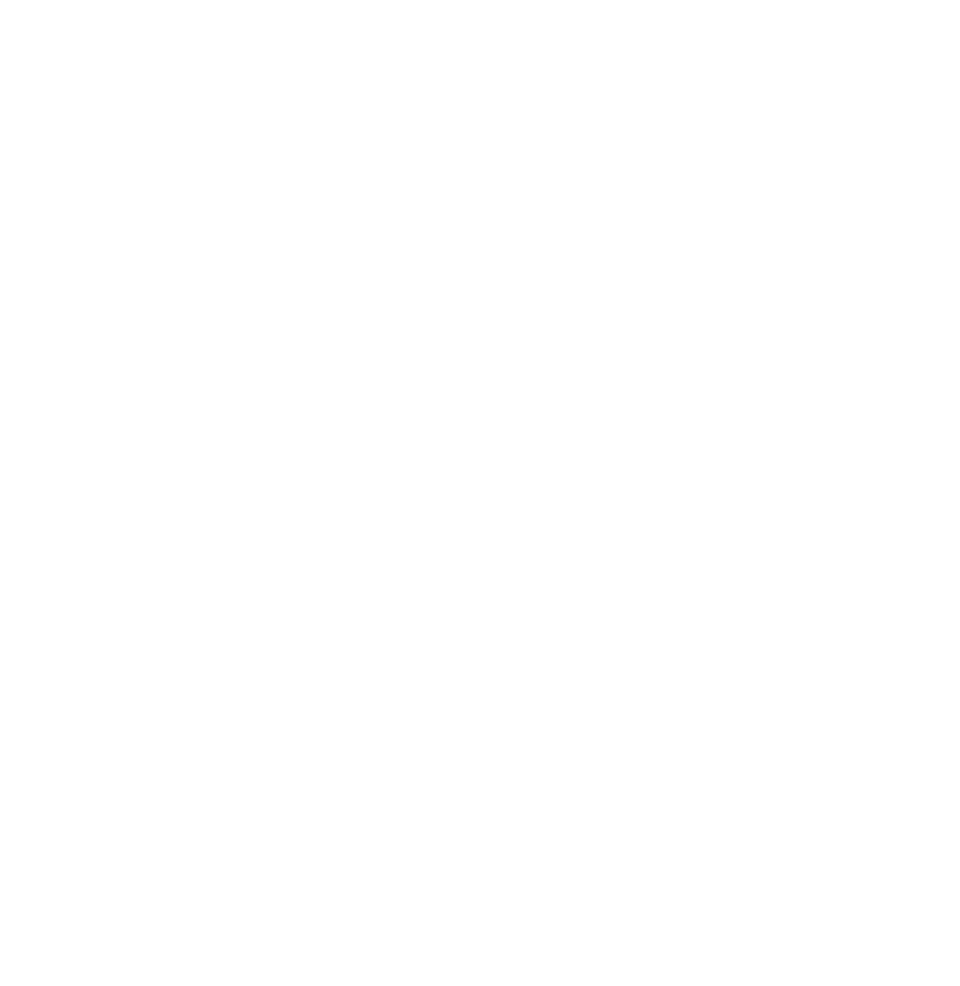
In this video, you can see the ductility of this system, with the two additional manual references that make the press brake ideal for processing particularly complex parts.
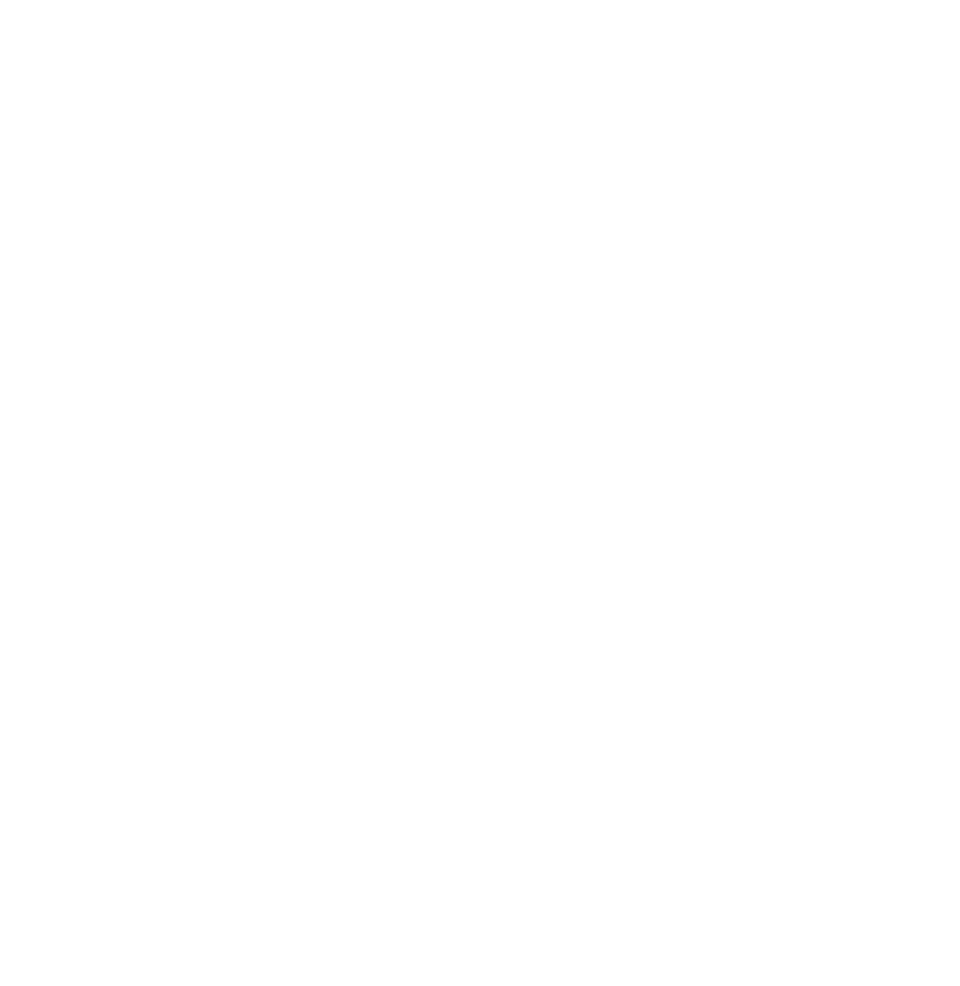
The upper pneumatic clamping system is of the Gasparini AirSlide type: it is a self-aligning system, available for European-type tools, which allows the vertical assembly and disassembly of press brake tools in a safe manner. This system allows automatic tool positioning and clamping, reducing tooling time and increasing overall machine productivity. The bottom clamping is also of the pneumatic type.
The press brake is equipped with two sliding front supports, mounted on a linear guide, adjustable in height and with a tool tray. They can be easily disengaged from the rail and moved due to their low weight. The support table measures 600 x 140 mm, and is covered with scratch-resistant polyethylene profiles. It can also support up to 500 kg.
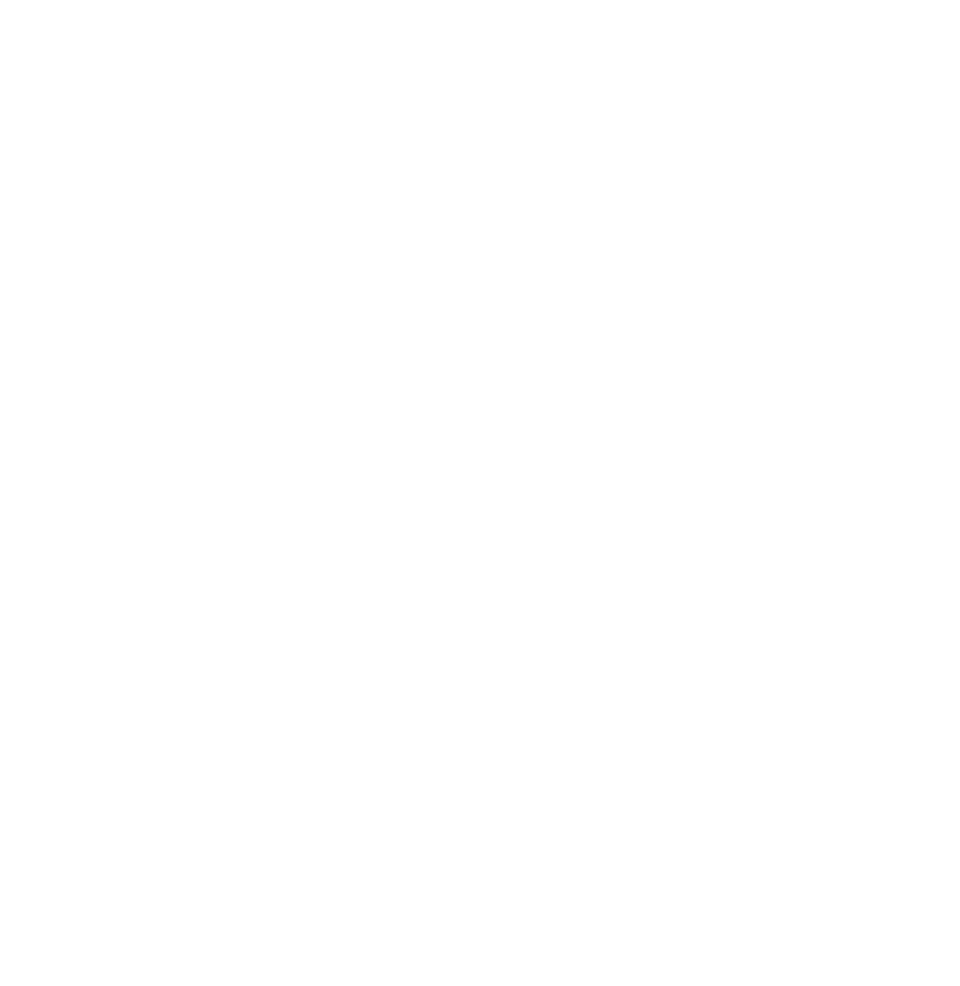
How to increase the safety of the press brake
The safety system is of the DSP-AP type and uses a visible laser beam that complies with EN12622 to protect the operator from the risk of crushing between punch and die. This represents an evolution from traditional light curtains or single-beam guards that do not comply with standards. Thanks to the device, it is possible to reduce the speed change point to as little as 4 mm from the plate, allowing the upper beam to move at high speed for a longer period and minimising the part of the bending sequence where speed is reduced.
This press brake features the ECO energy-saving and Industry 4.0 packages.
It has also been equipped with a standard foot pedal.
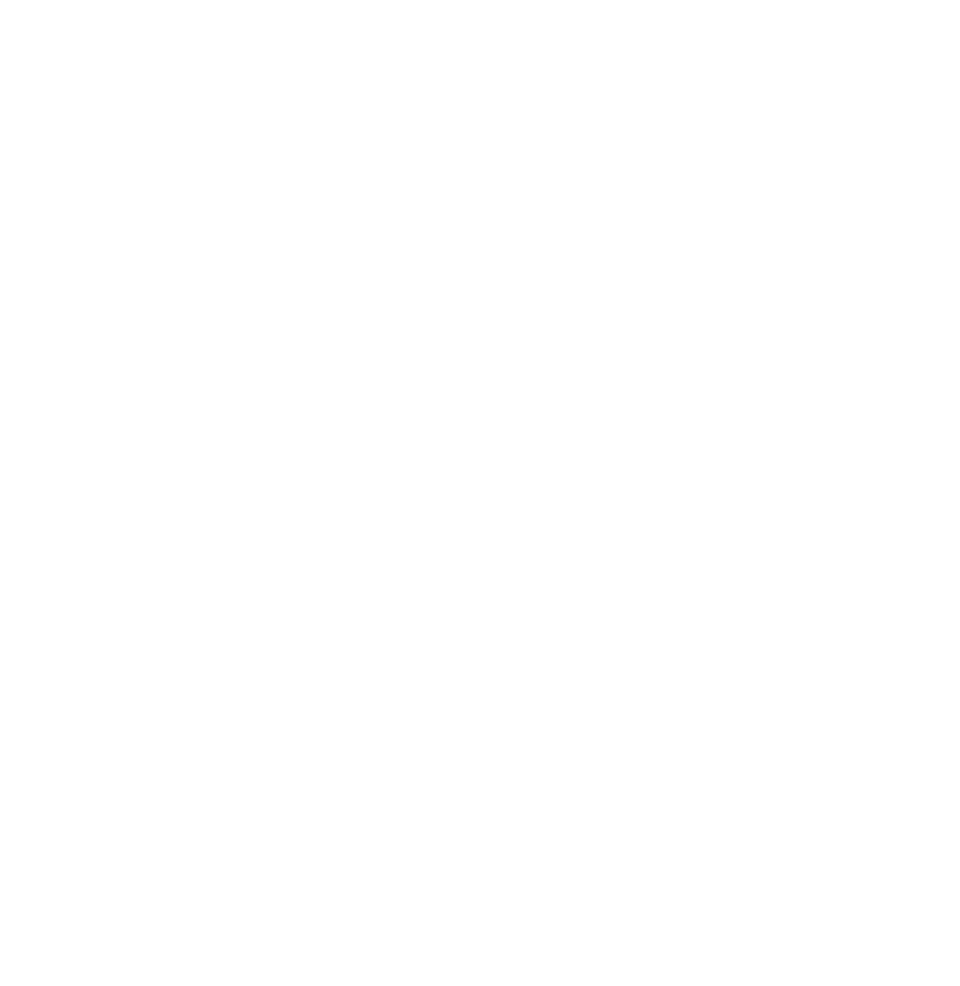