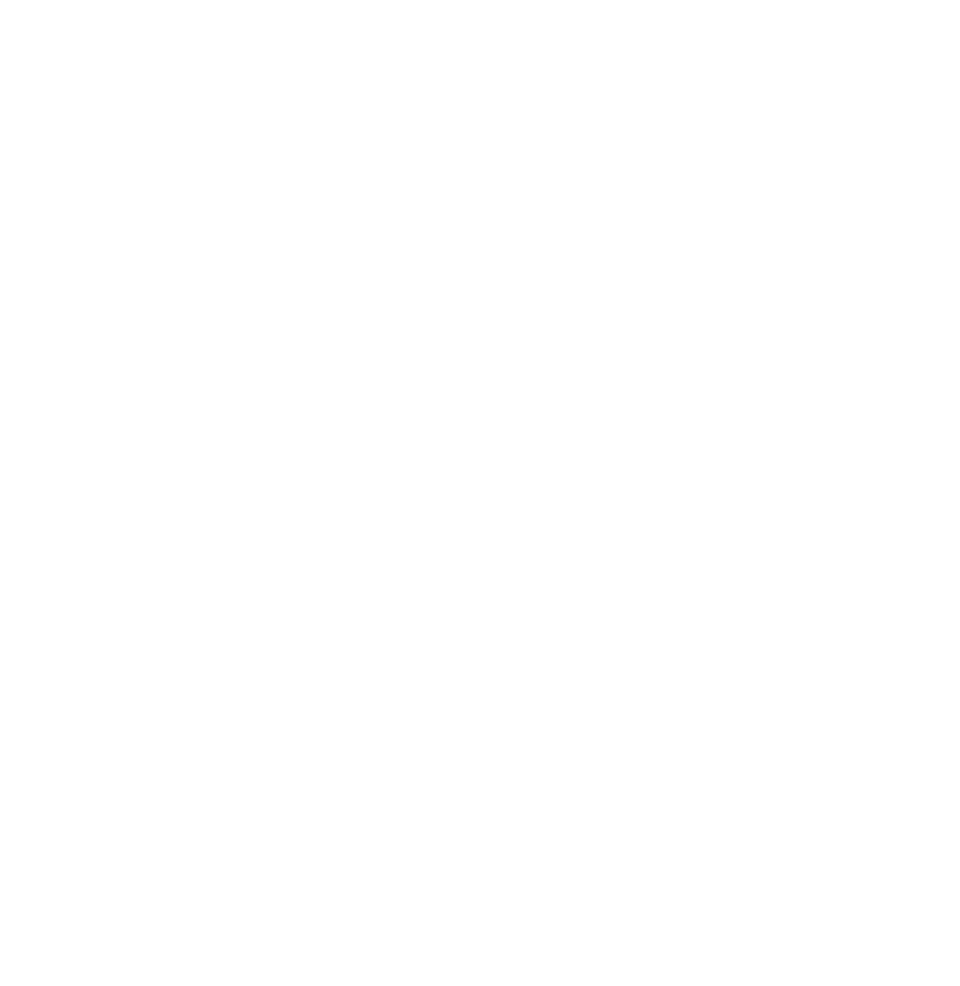
The main technical features of the press brake
The open-height is 400 mm and the Y axis stroke is 200 mm. The machine is characterized by the E-Reflex deformation compensation system.
This press brake has been configured with the Design Next and is equipped with the Iris Plus laser safety system with PLC, with automatic positioning of the Lazer Safe photocells.
It features the Stand-by energy saving system, equipped with a device that monitors machine activity and switches off the engine after a certain period of inactivity. As soon as work is resumed, the hydraulic circuit is immediately operational again.
Furthermore, an electrical interface has been set up for the operator-robot configuration (with photocells and sensorized references).
Which accessories to choose for press brake automation
The customer chose to equip the press brake with the Delem DA-66T CNC mounted on a hanging arm from above and the Delem Profile Lite TL 2D offline software, which guarantee ease of use and cutting-edge technology. The touch screen allows you to access the proven user interface and navigate directly between programming and production.
In addition, communication standards compliant with the Intelligent Factory models of Industry 4.0 have been installed.
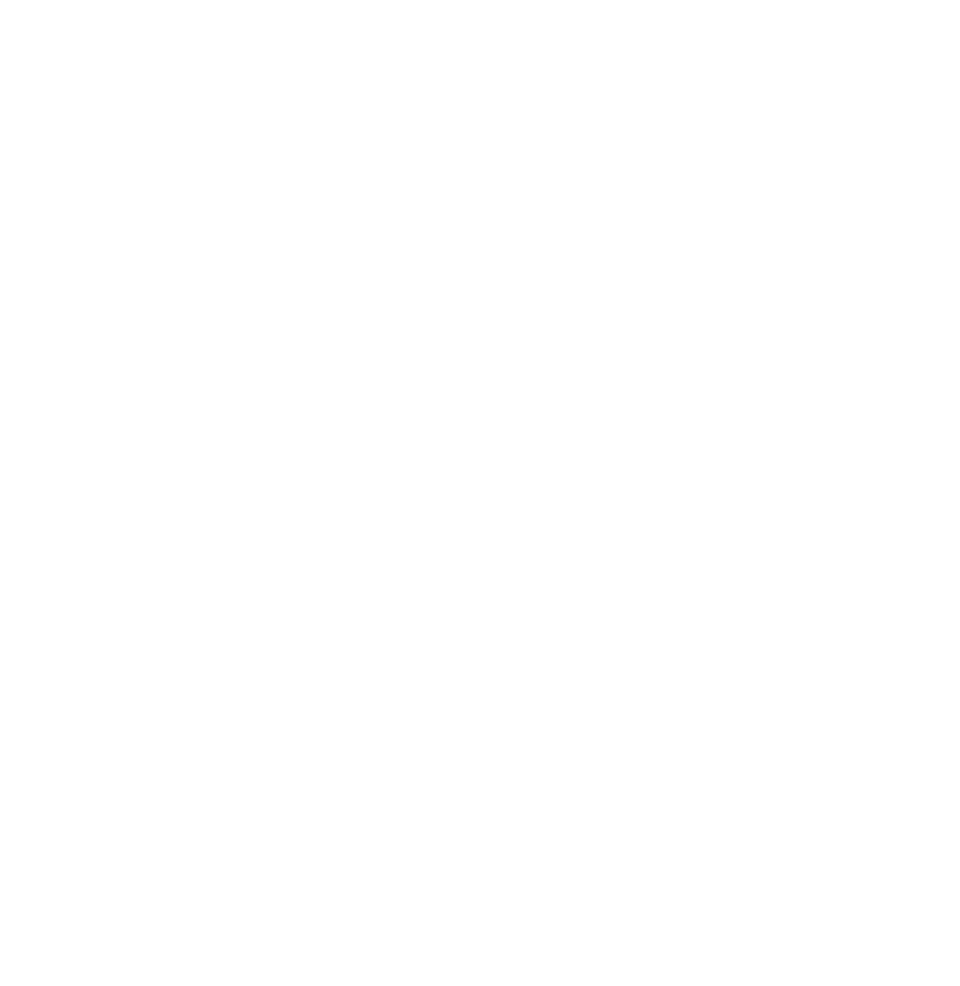
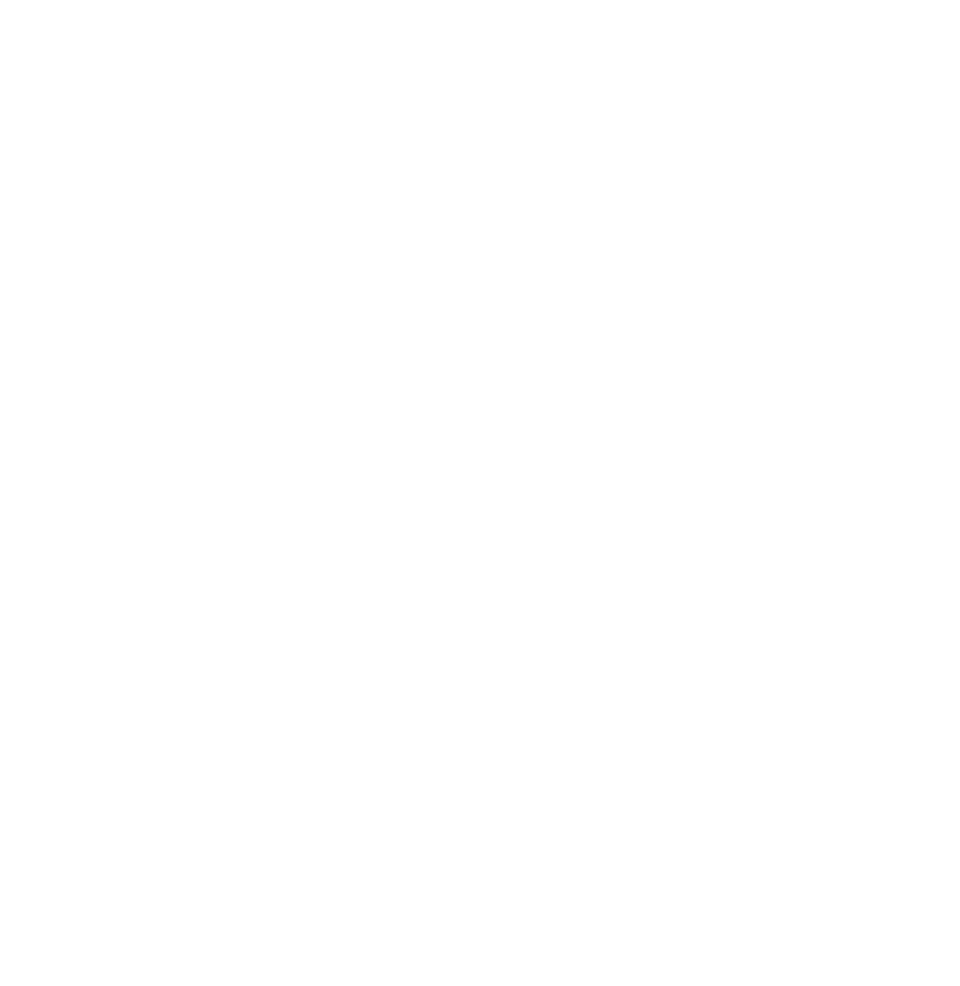
Increasing the speed of bending work: which accessories should be provided
The Seriveneta press brake has tool adapters with quick locking with Toolever self-aligning lever with a height of 100 mm and manual lower clamping.
The Toolever tool adapters, thanks to the lever operation without tools, allow a huge saving of time compared to traditional screw clamps. The height of 100 mm, equal to that of the manual screw tool adapters, does not require reprogramming of the CNC. The crowning wedge can be adjusted from the front, and allows the intermediates to be aligned close to each other.
Precision and ergonomics of the press during bending: how we achieved them
The backgauge has 4 axes (X-R-Z1-Z2) controlled by CNC, which in addition to the two standard axes also has the Z1 and Z2 axes. It also features an additional stop on a backgauge reference for increased contact depth during the bending phase.
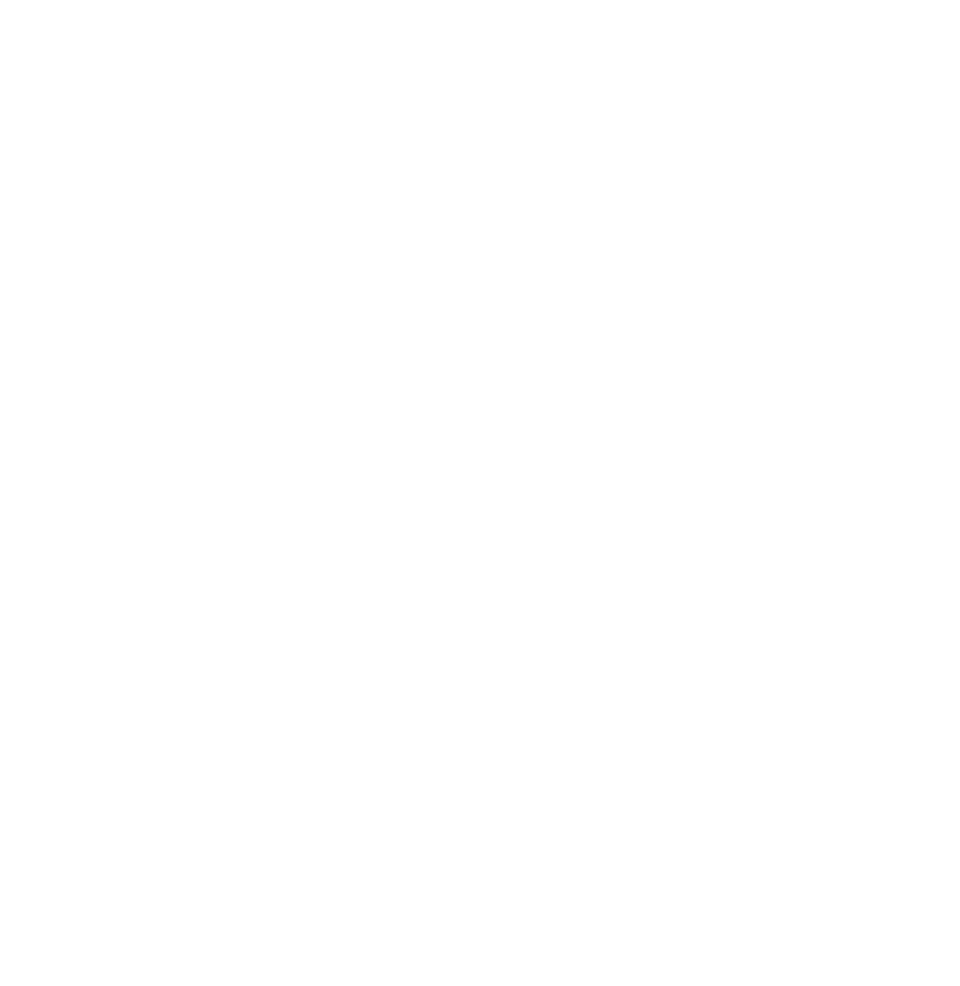
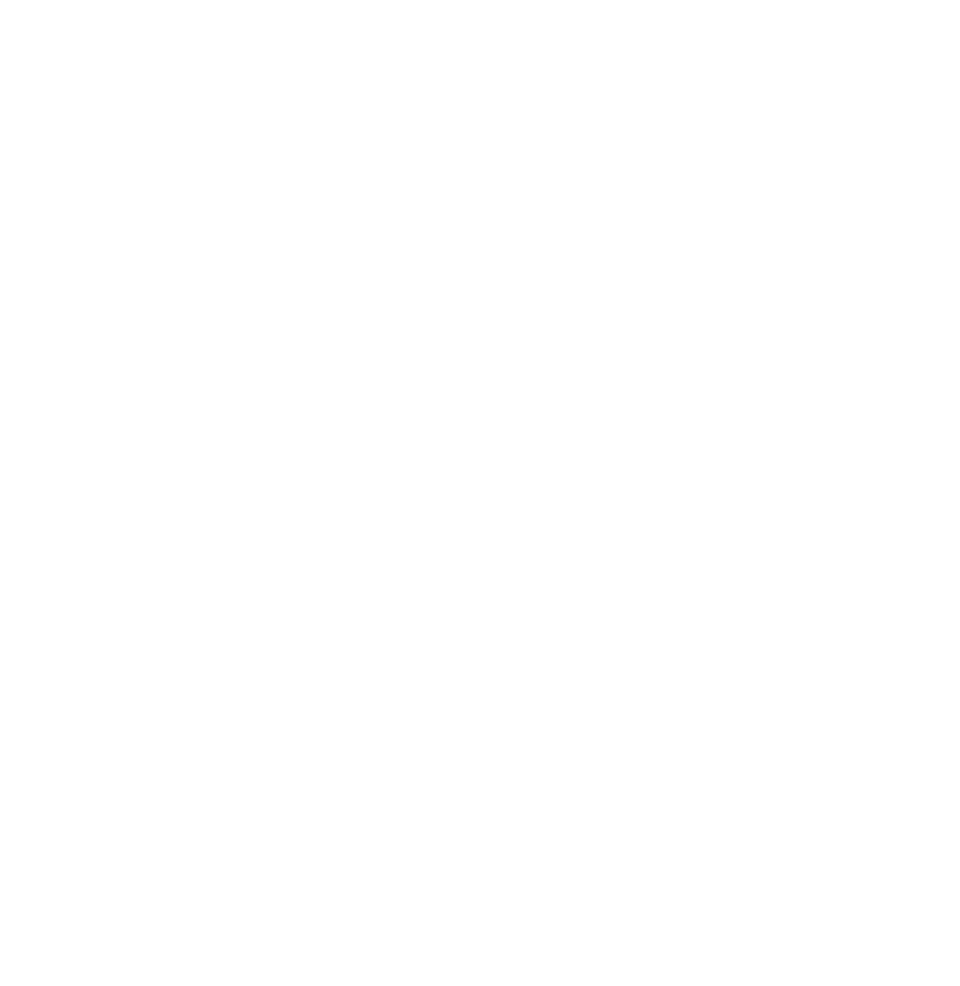
Customisation of the press requested by the customer
Finally, the following have been added to the accessory package:
- two standard front support arms
- standard foot pedal
- tool cabinet
- LED lighting of the work area