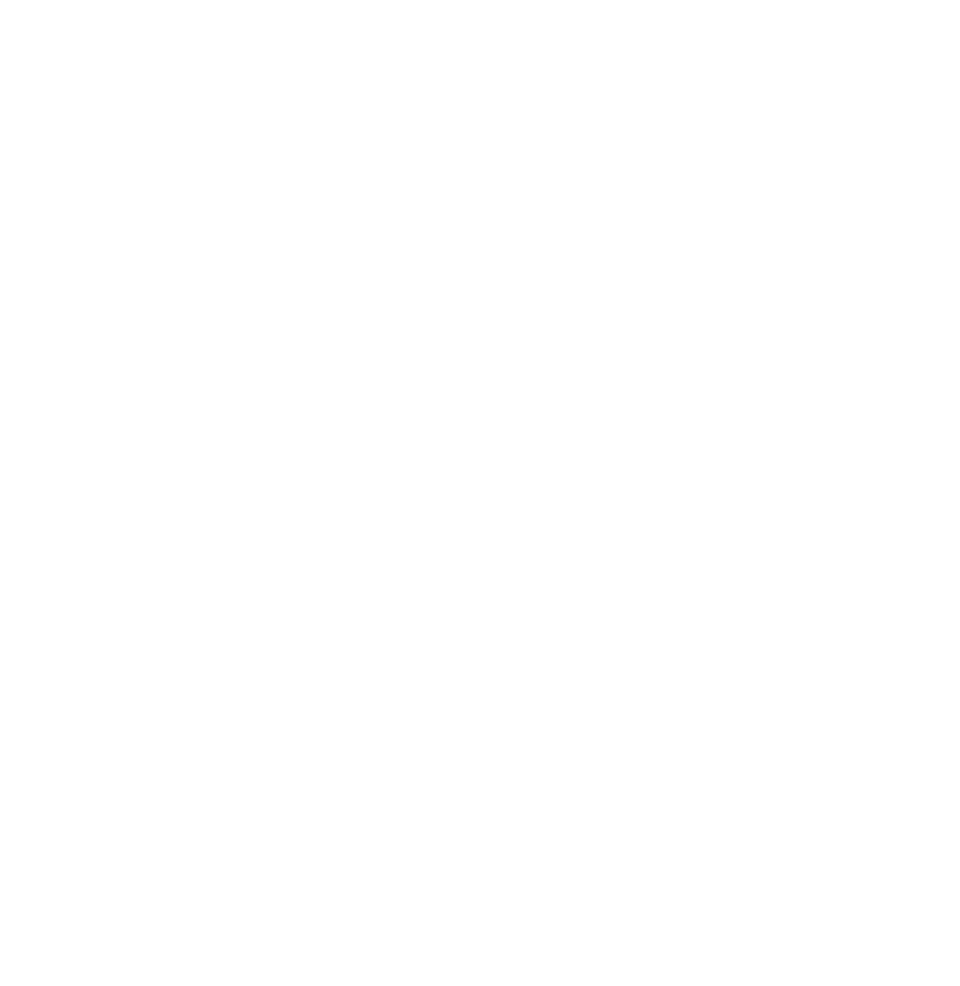
The main technical features of the press brake
This press brake is equipped with the Gasparini Adaptive Crowning System and the E-Reflex Side Frames Deflection Compensation System. Together, these two systems provide excellent results in terms of quality, precision and repeatability of the parts to be bent.
The CNC is the Delem DA-66S, with Delem Profile Lite SL 2D offline software.
DA-66S features:
- High-resolution 24″ touch screen (16:9)
- 3D visualisation of bending sequence
- 2D programming
- DXF file import
- 3D visualisation of offline programme
- Offline software included: Profile-SL
- Industry 4.0 package
The choice of pneumatic clamping system
As far as the clamping system is concerned, the 110 mm high Gasparini AirSlide pneumatic clamp for European type tools was chosen for the upper part of the machine. This self-aligning system allows the vertical assembly and disassembly of the press brake tools in complete safety. The automatic alignment function positions and secures the tools, reducing set-up times and increasing productivity.
The bottom clamping is also pneumatic.
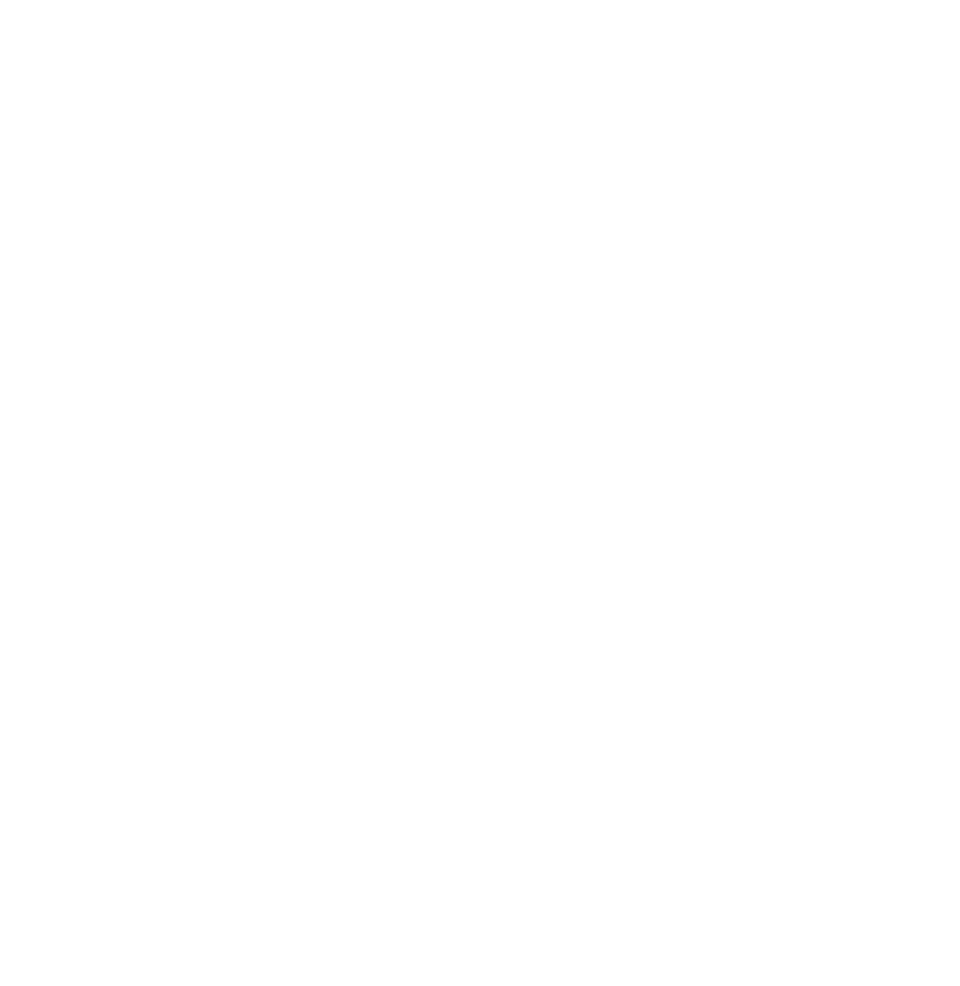
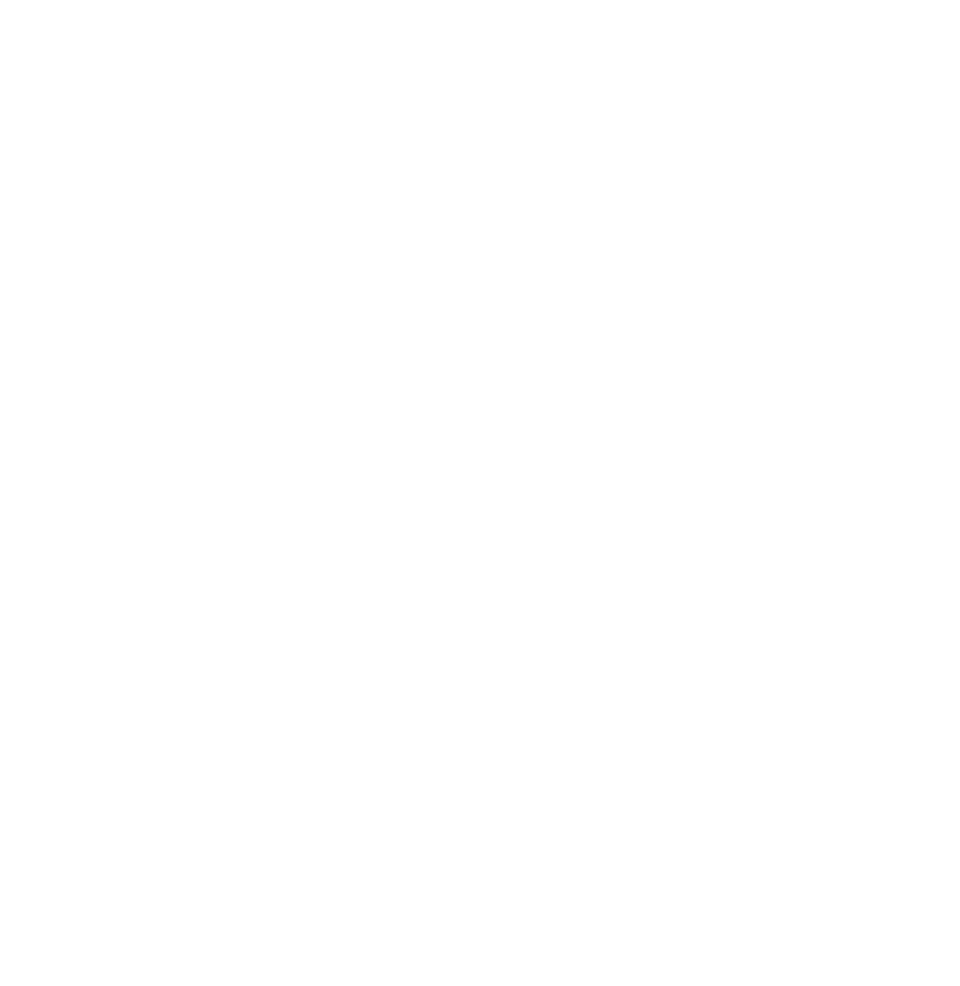
Precision and ergonomics of the press during bending: how we achieved them
The backgauge has 5 CNC-controlled axes (X-R-Z1-Z2-X6), and is equipped with two retractile back supports and an additional stop.
The two retractile supports are equipped with polyethylene profiles and allow even the thinnest sheets to be supported without scratching their surfaces.
Thanks to the combination of these elements, the bender achieves the highest level of precision and ergonomics during the bending process.
Laser safety system
This press brake is equipped with the Iris Plus laser safety system with PLC.
This safety system uses a two-dimensional matrix sensor to read the entire area around the punch tip.
With an optical resolution of only 2 mm, it allows the speed change point to be set at 0 mm from the sheet. The cycle time is greatly reduced: up to 3 seconds saved per bend. The maximum distance between the systems is 15 m.
The system has been implemented with Lazer Safe motorised photocell supports.
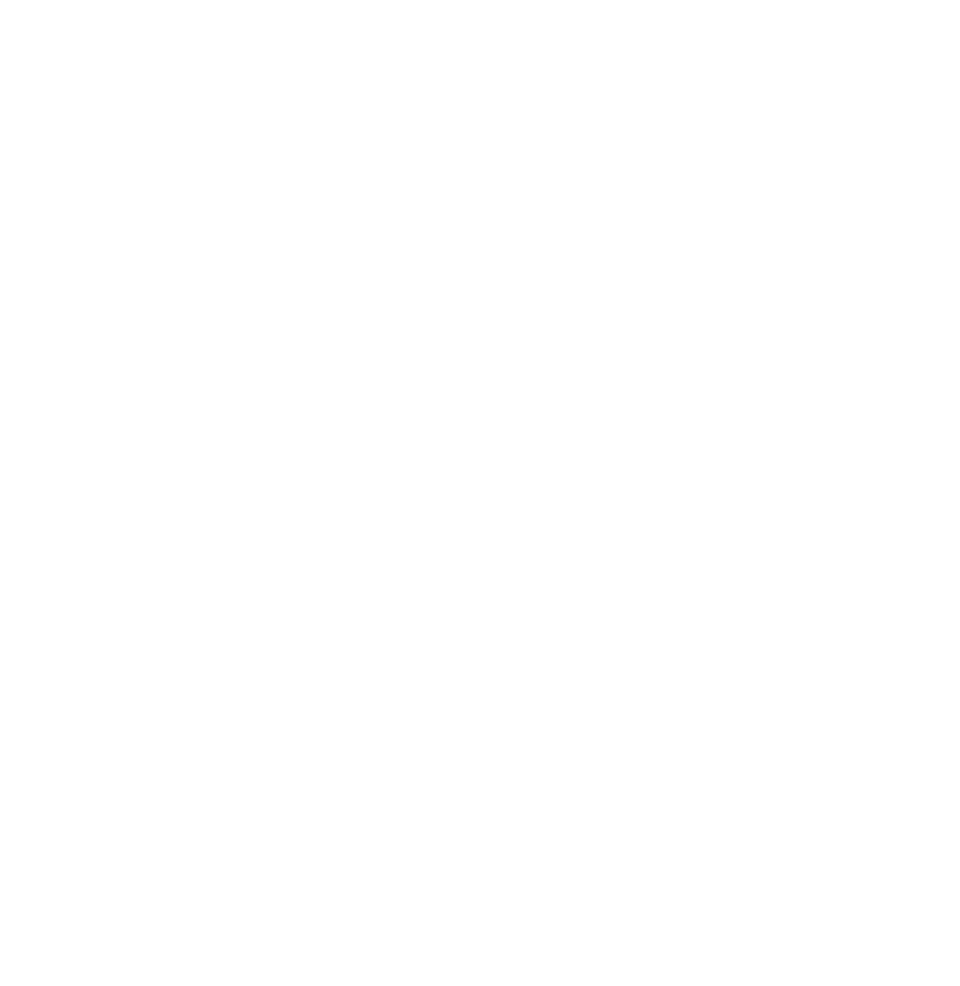
Press customisations required by metal carpentry
In addition to the main systems and accessories, this press brake features:
- ECO energy-saving package
- Self-centring table with 60 mm width
- GPS4 mechanical set-up
- 2 sliding front supports
- Drive bar for tool positioning
- Standard foot pedal
- LED work area lighting