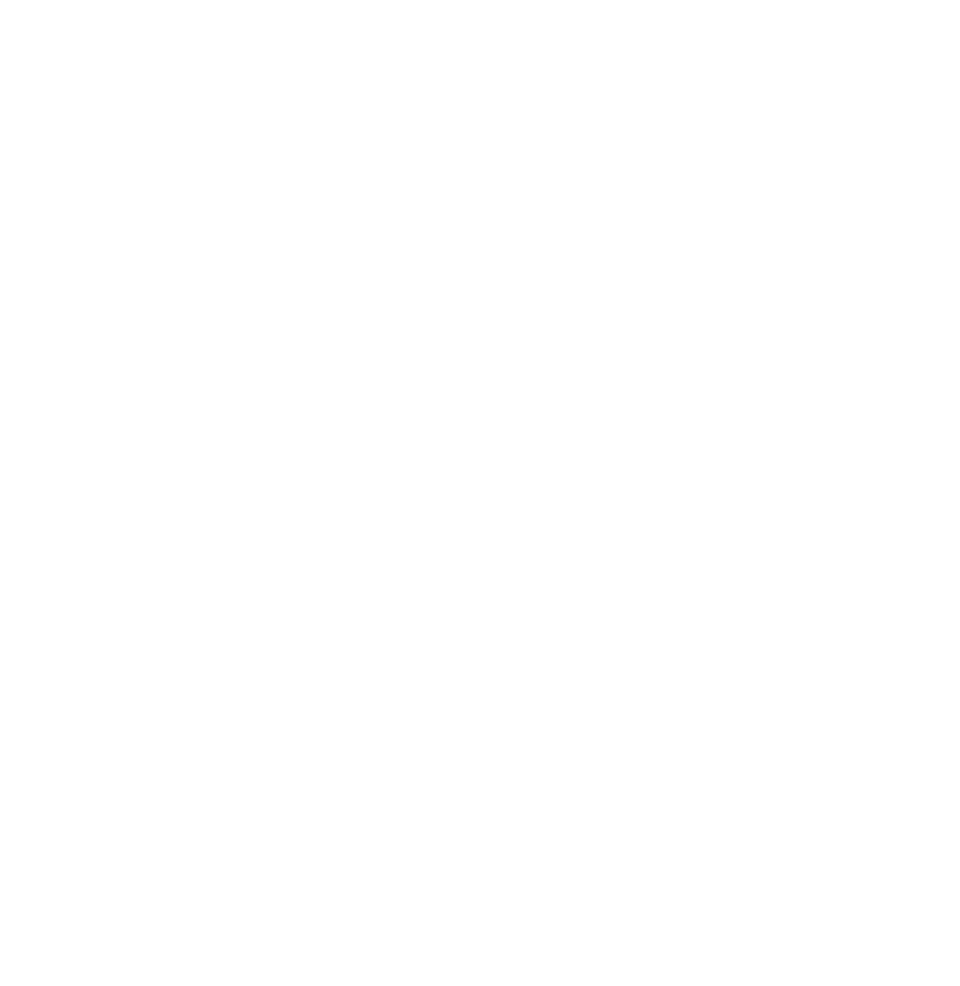
The main technical features of the press brake
This machine was built with our Easy design. The bench-cross span is 700 mm, the Y-axis travel is 300 mm and the working area is equipped with LED lighting.
In addition to the automatic hydraulic crowning system, it is also equipped with the E-Reflex deformation compensation system: the combination of these two technologies allows for maximum precision during the machining phase. The E-Reflex system monitors the bending of the structure through a series of sensors located both inside the press brake and in the hydraulic system. These devices detect any anomalies and compare the position of the crosshead with the oil pressure to determine the actual position of the punch, regardless of deflections.
Automation and ergonomics in the press brake: how we achieved them
CEB’s press brake was implemented with the Industry 4.0 package and the Tele-Link remote service function. It features a Delem CNC type DA-66T and the offline software is Delem Profile Lite TL 2D.
It was also equipped with a standard foot pedal and two sliding front support arms. These brackets are sliding, height-adjustable accessories, mounted on a linear rail, with a tool tray. They can be easily detached from the rail if required, and thanks to their low weight they can be moved with very little effort. The shelf measures 600 x 140 mm, is covered with scratch-resistant polyethylene profiles and can support up to 500 kg.
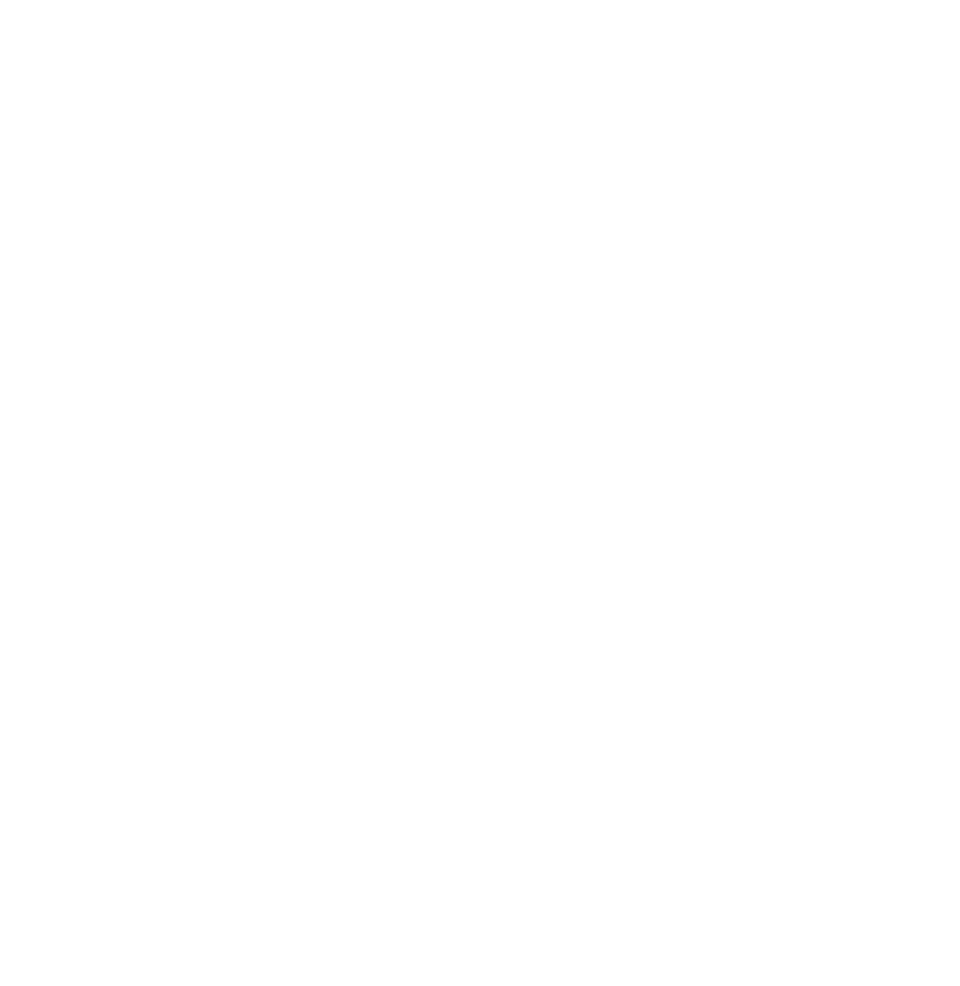
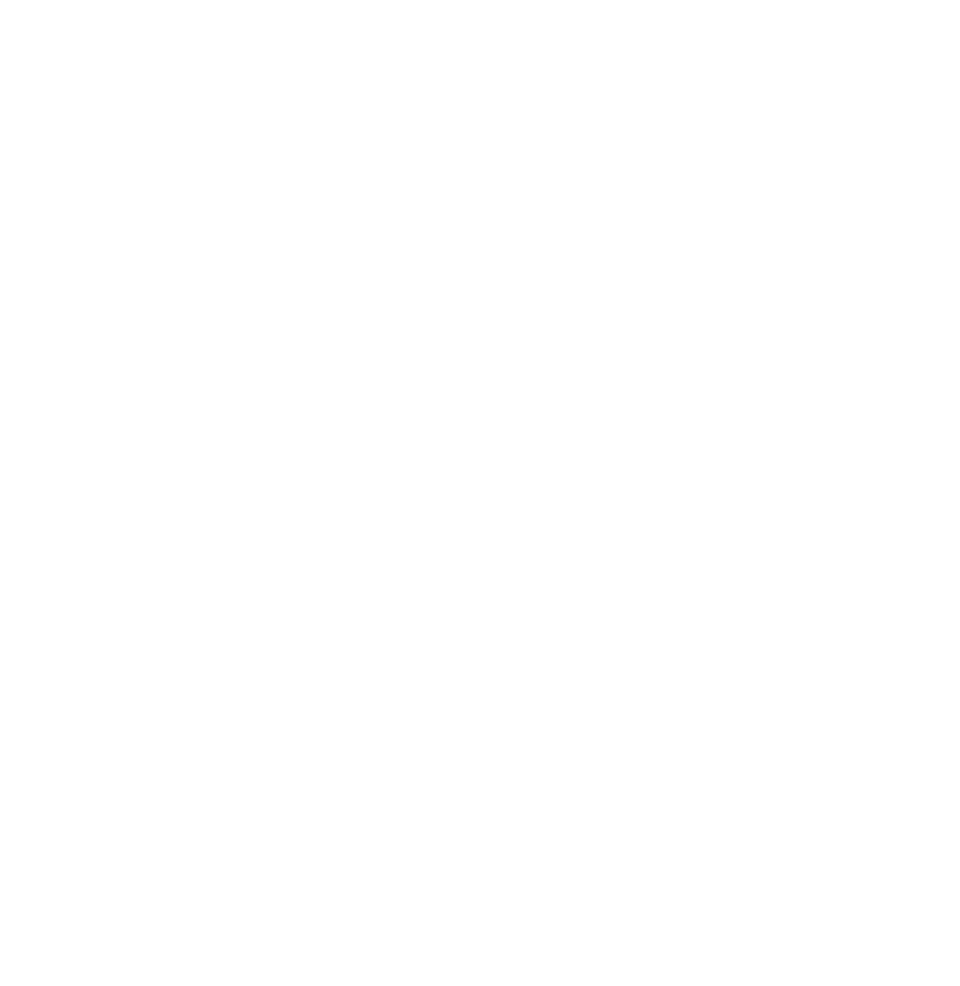
The upper pneumatic clamping system is a Gasparini AirSlide type with a height of 300 mm: it is a self-aligning system, available for European-type tools, which allows the vertical assembly and disassembly of press brake tools in a safe manner. This system allows automatic tool positioning and clamping, reducing tooling time and increasing overall machine productivity. The bottom clamping is also of the pneumatic type.
The backgauge is 5-axis (X-R-Z1-Z2-X6) CNC-controlled, which in addition to the two standard axes also features the Z1 and Z2 axes. It features an additional stop on a backgauge reference for an increased depth of support during the bending process.
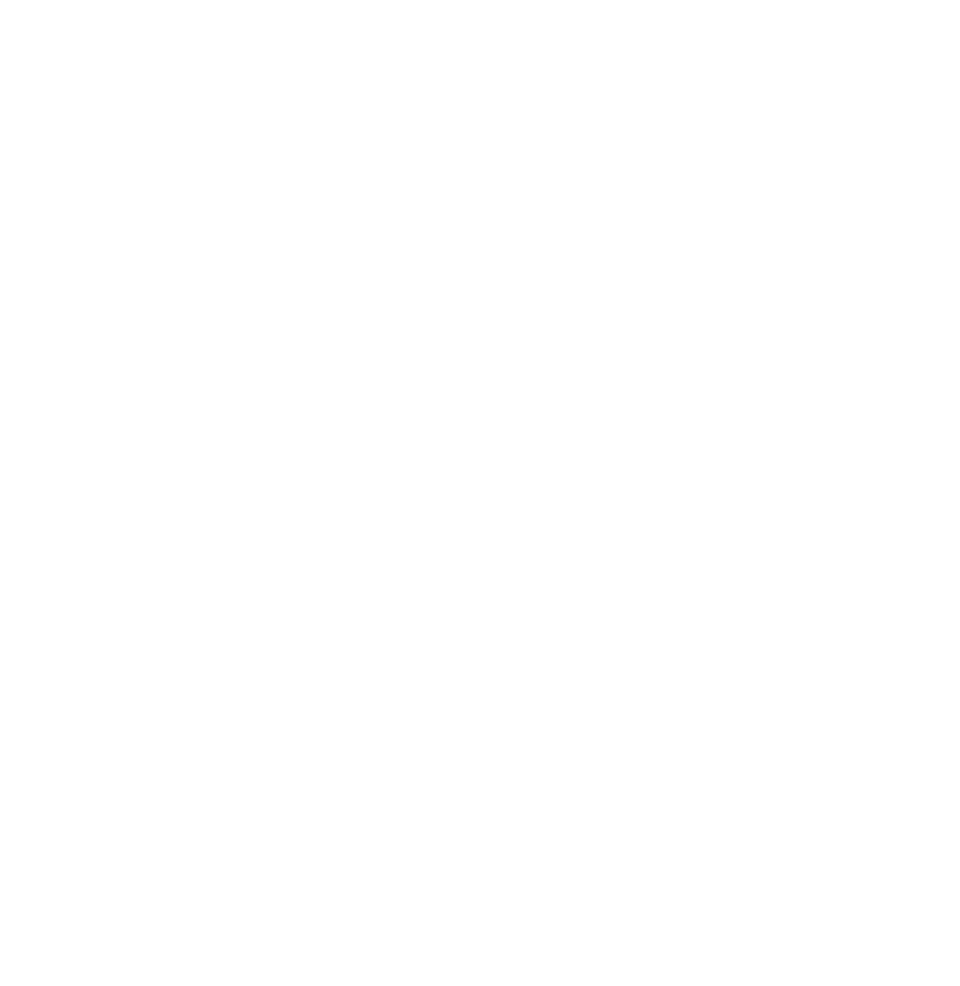
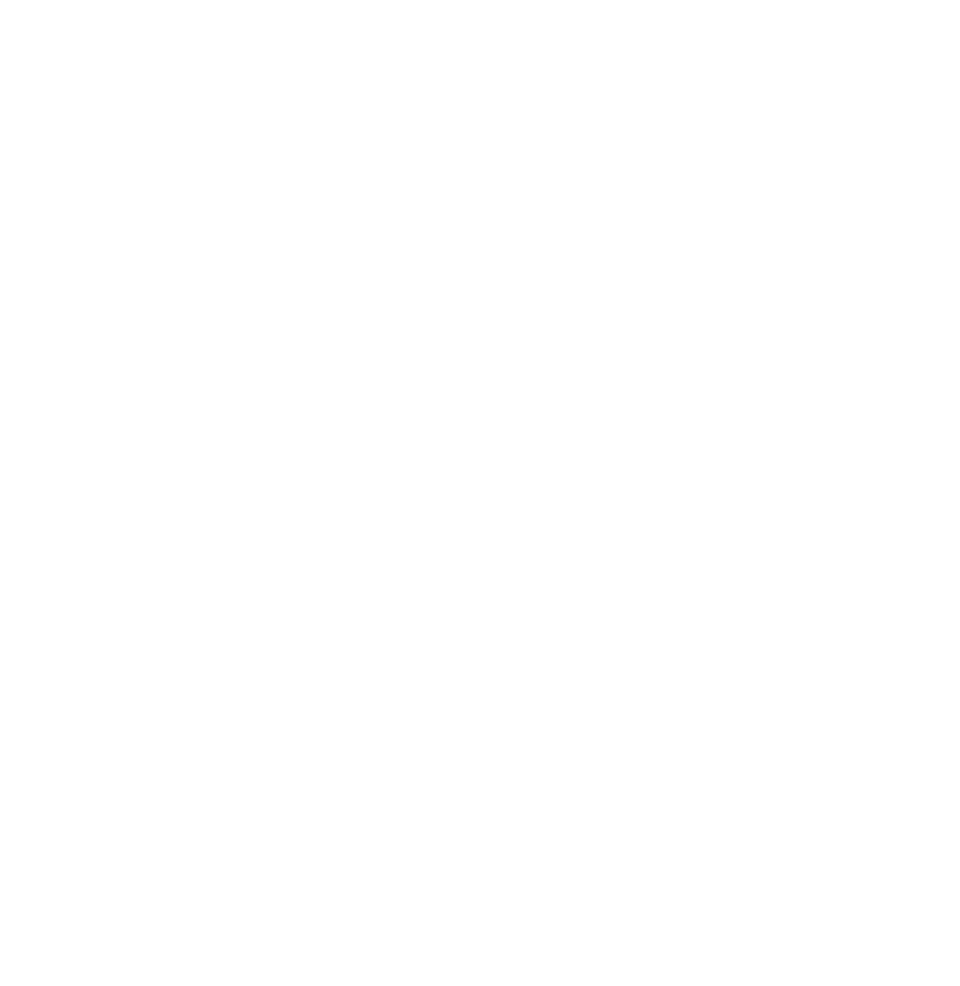
Energy savings in the press brake
For this press brake, CEB chose the ECO energy-saving package: it is based on the continuous control of the machine’s main motor via a vector inverter. Instead of running continuously at a constant speed, the main motor is regulated continuously. This makes it possible to run the pump at low speed when low flow is required, and to accelerate to maximum performance when full flow and pressure are needed.
The safety system is of the IRIS laser type with PLC. This is an optical guarding system that works in conjunction with image processing: it consists of a laser transmitter and receiver mounted on the upper crossbar of the press brake. This system uses a two-dimensional matrix sensor to read the entire area around the punch tip.
Adaptive Environment Sensing (AES) and automatic thickness detection
The technology of this device makes it automatically adaptable to environmental conditions, guaranteeing the performance of the machine. The camera filters the image even in the event of beam turbulence around the punch. Moreover, thanks to the communication with the CNC, it is not necessary to perform the thickness acquisition cycle.
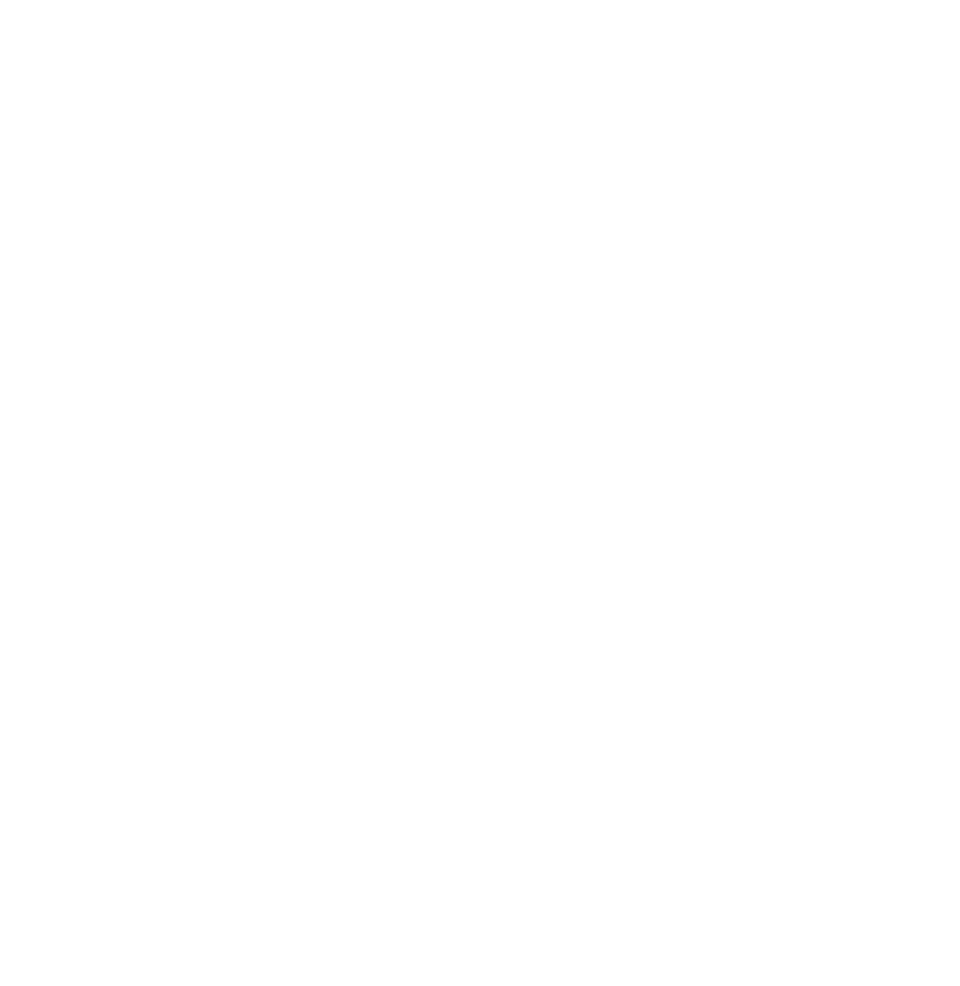
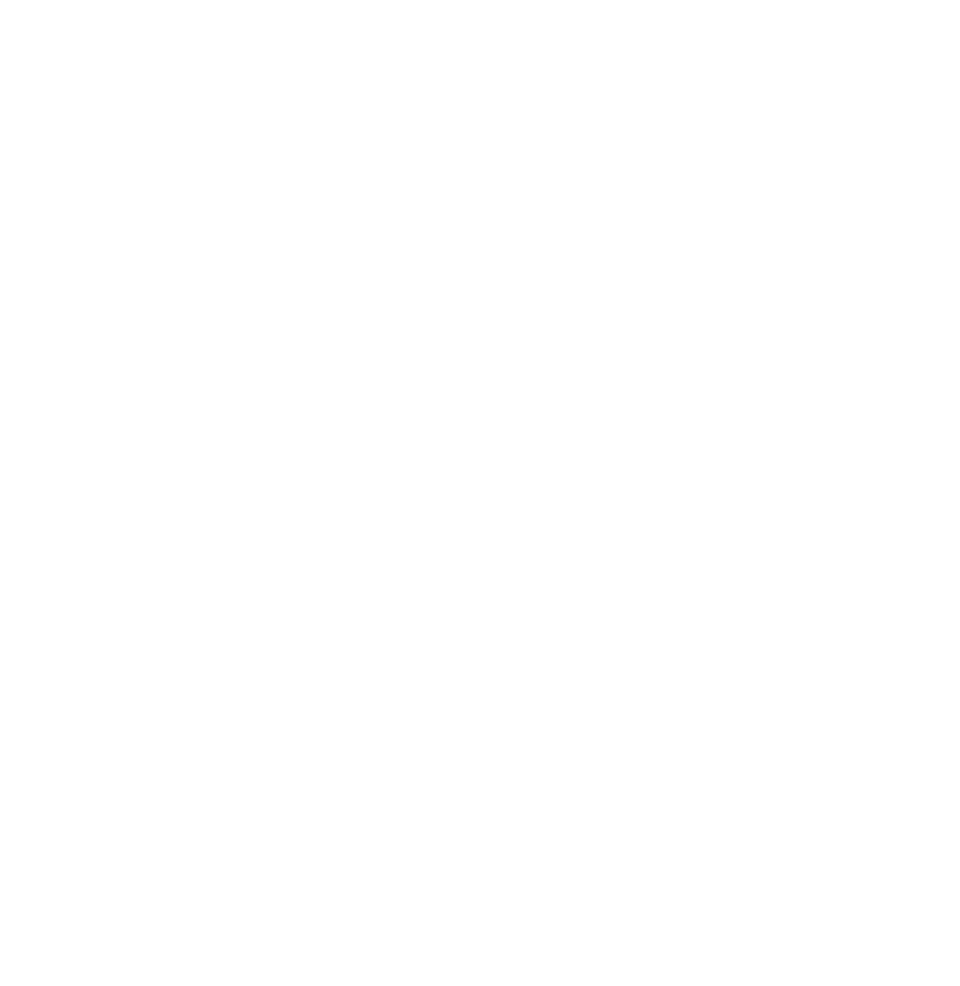
This machine was equipped with the Drive Bar, a bar of coloured LED lights, controlled directly from the CNC. The blue light indicates to the operator where to install the upper tools; the green light indicates where the next active station will be. This allows the operator to position himself directly at the indicated point for the next bend, without hesitation, saving considerable time.