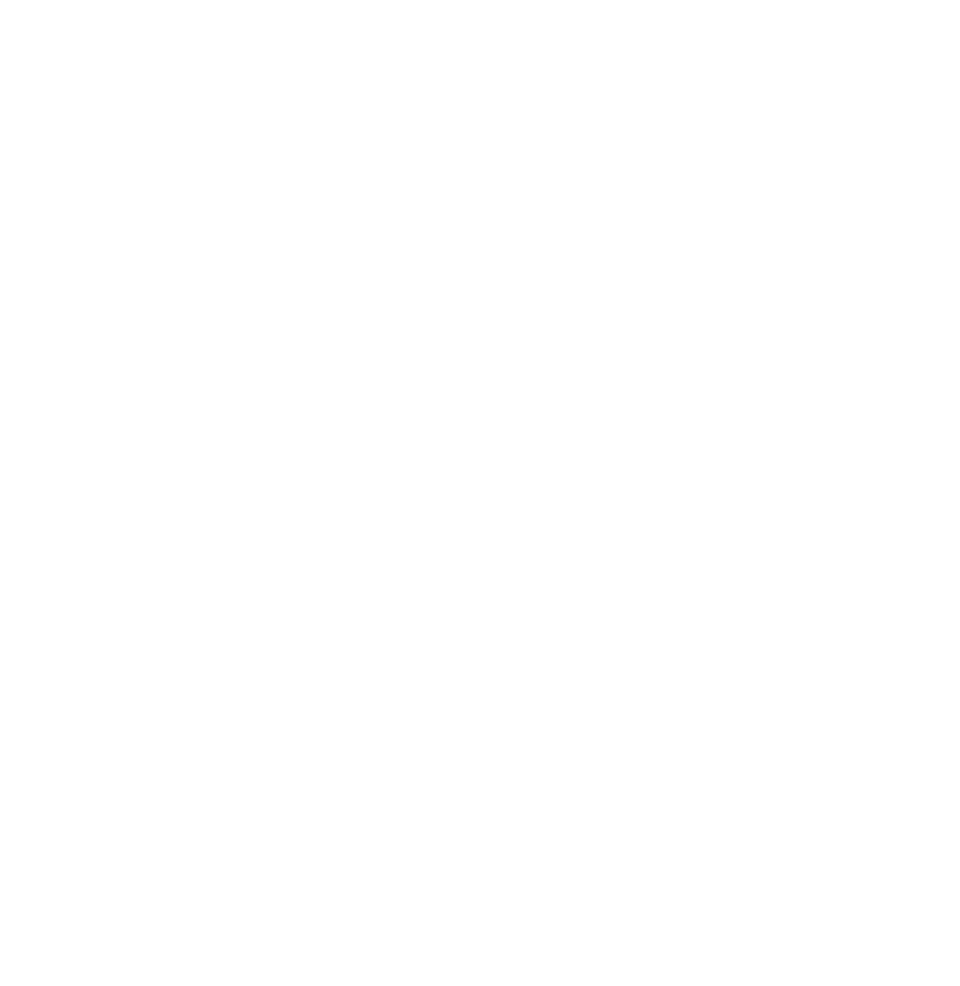
The main technical features of the press brake
In both cases, the open-height is 500 mm, with a Y-axis travel of 300 mm to make it easy to machine workpieces while also machining medium-sized boxed parts. Under the production conditions for which the two machines were designed, tool changes in the upper crosshead are not frequent, so manual-type intermediates with European-type Toolever clamps were chosen. While pneumatic clamping, also of the European type, was adopted for the dies.
Precision, ergonomics and press safety during bending: how we achieved them
The backgauge has 5 axes (X-R-Z1-Z2-X6) controlled by CNC. To the standard axes therefore, Z1 and Z2 were added to be able to move the back references laterally to facilitate positioning of parts of different lengths and working by stations. In addition, the X6 axis was also added to be able to handle parts with different support points. This also makes it possible to make conical bends of up to 75°. The front and foot supports are standard, and for both the CNC is the ESA S 660 W. Both Tele-Link remote service functionality and communication standards conforming to Industry 4.0 Intelligent Factory models are also installed.
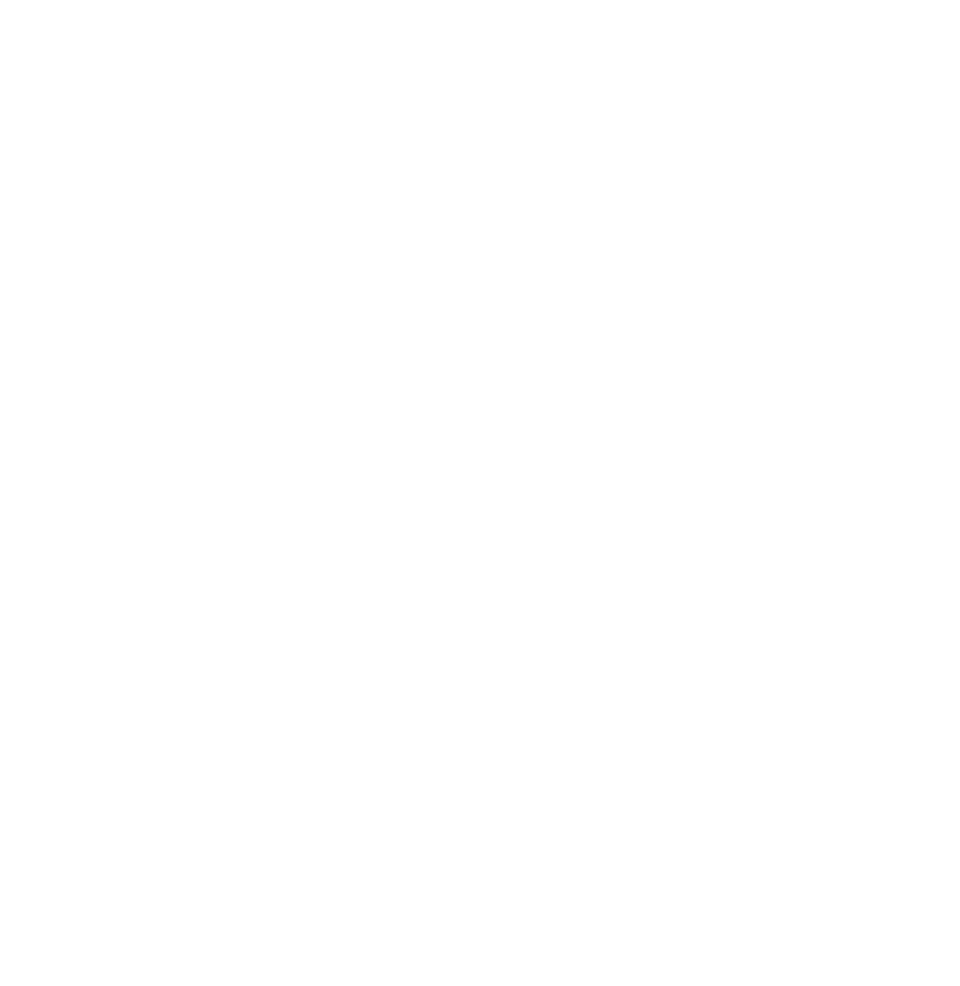
How to reduce waste and increase productivity in the press brake
To reduce waste and increase productivity, we implemented the two machines with the ECO energy-saving system, which includes inverter control of the main motor. In this way, the motor is activated only when needed, providing only the power necessary for the bending process. During the production cycle, oil stress and energy waste are reduced by up to 50% compared with the standard version.
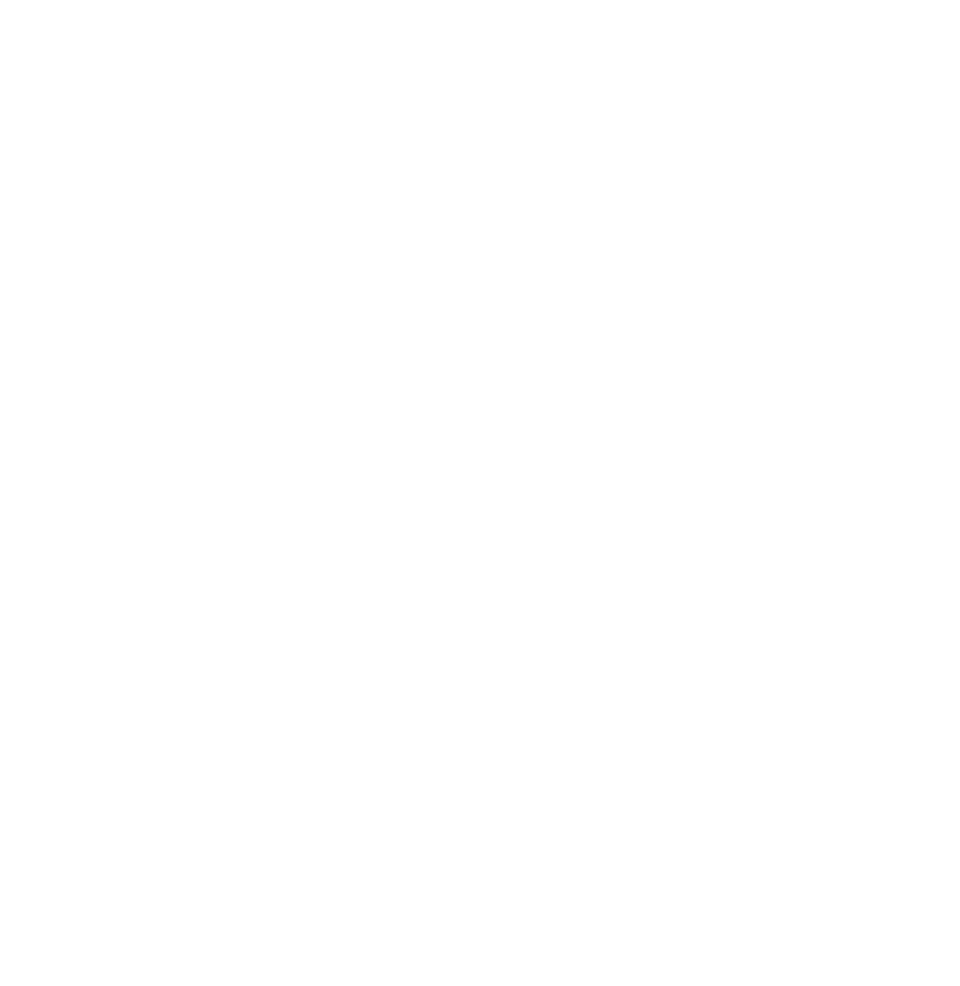
The machines are then equipped with Gasparini Adaptive Crowning System: the patented system in which a sensor located in the upper beam detects the deflection of the latter since bending begins. The CNC drives the pistons in the lower crossbeam until the measurement of the second sensor placed on it is equal to that of the first. In this way the two crossbars are perfectly parallel and allow total control of the angle, guaranteeing maximum precision and absolute repeatability with all types of material. There is no need to set any value, as the machine gets it directly from its own sensors.