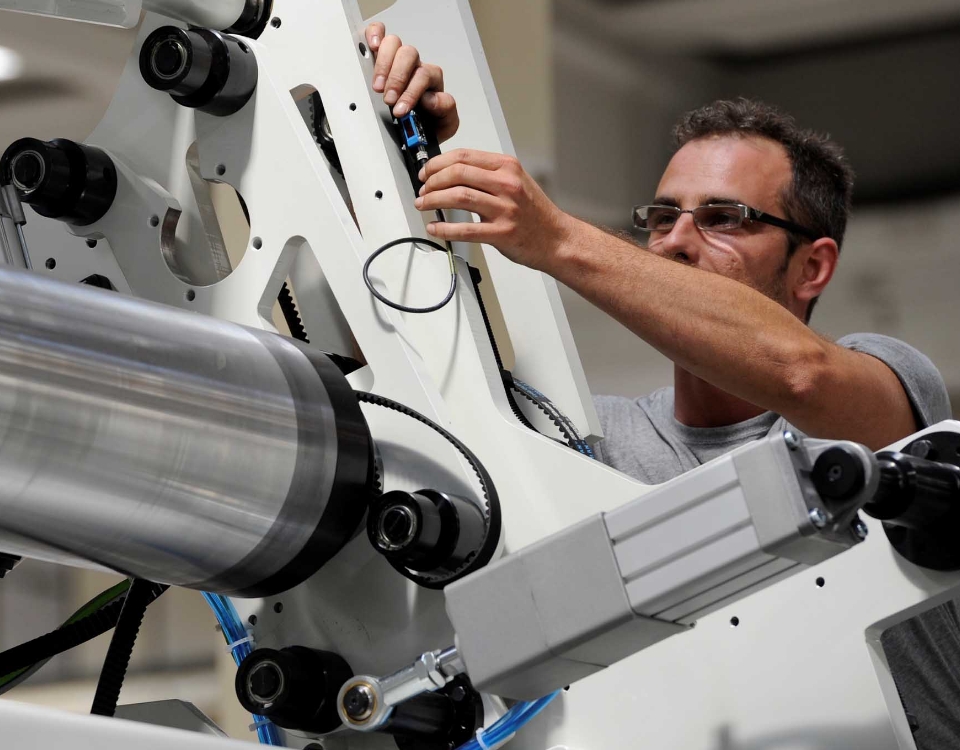
X-Press 80/2500
The press brake is designed with our Easy design. The open-height is 400 mm, the stroke is 200 mm and the working area is equipped with LED lighting. This machine has been implemented with the Industry 4.0 package and the Tele-Link remote assistance function. Its Delem CNC technology is DA-66T, while the offline software is Delem Profile Lite TL 2D.
This press brake is equipped with the hydraulic bending system, which works in conjunction with the E-Reflex deformation compensation system, which monitors the bending of the structure through a network of sensors located both inside the machine and in the hydraulic system. These sensors detect any anomalies and compare the position of the crossbar with the oil pressure to determine the actual position of the punch, regardless of deformations.
The customer’s choice of clamping system fell on the Toolever self-aligning lever quick clamping tool adapter with a height of 100 mm. These are quick-release lever-operated tools without tools, thanks to which a clear time saving can be achieved compared to traditional screw clamps.
Features:
- Height 100 mm: no programme changes required.
- Front centring wedges: tool adapter contact without gaps.
- Double clamping with front clamping for mounting inverted tools.
- Opening and closing without special tools, just an ordinary spanner or screwdriver.
- Tools remain in a safe position even with the locks open.
- Self-aligning: during closing, the punches are lifted and pushed against the tool adapter, eliminating the need for preliminary bending.
- They also support segmented punches up to 10 mm.
The lower clamping is a manual type.
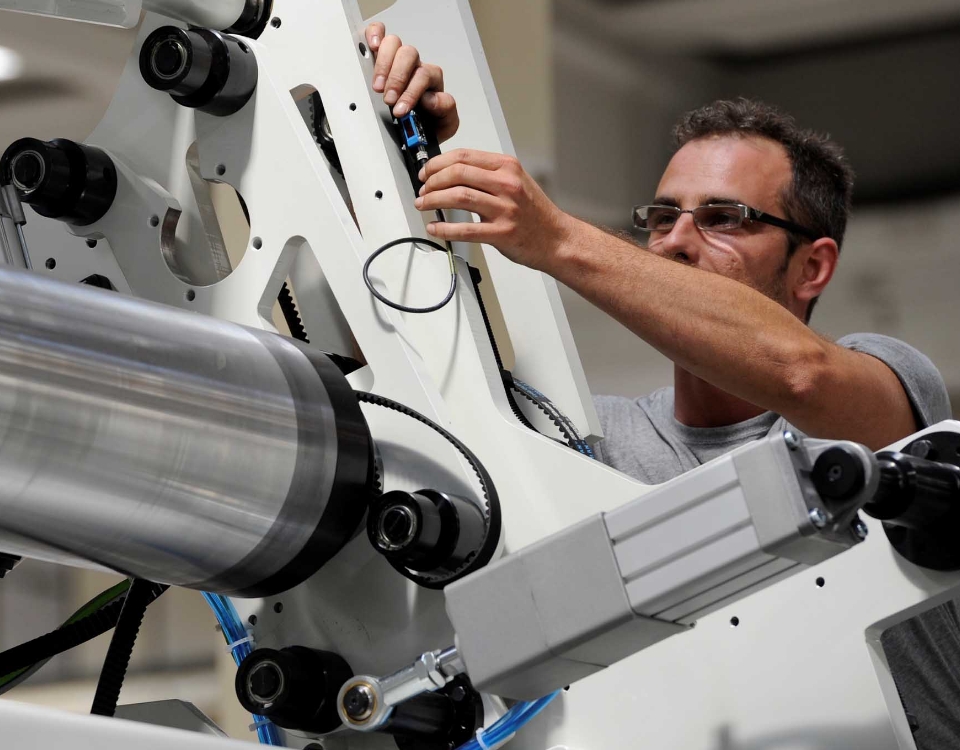
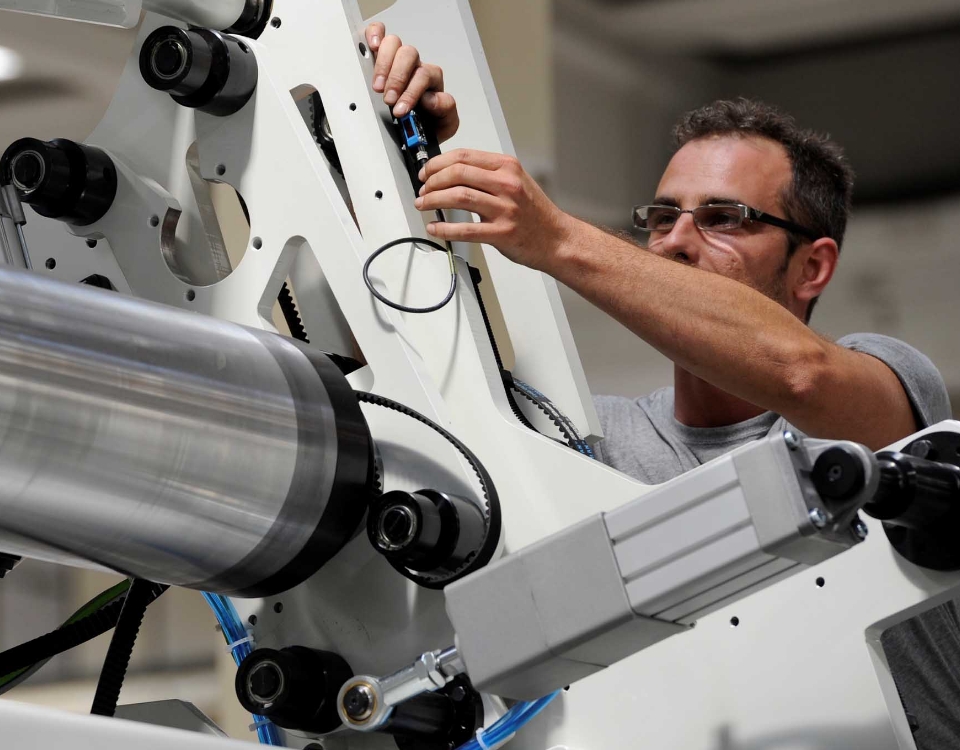
The backgauge has 6 axes (X-R-Z1-Z2-X5-X6) controlled by CNC. It has also been implemented with the addition of a stop on one of the references.
The safety system adopted is the DSP-AP. It generates a visible laser beam conforming to EN12622. The beam protects the operator from the danger of crushing between punch and die. With this device it is possible to position the speed change point only 4 mm away from the sheet, which allows the upper beam to maintain a high speed for a longer time, minimising the part of the bending process where speed is reduced.
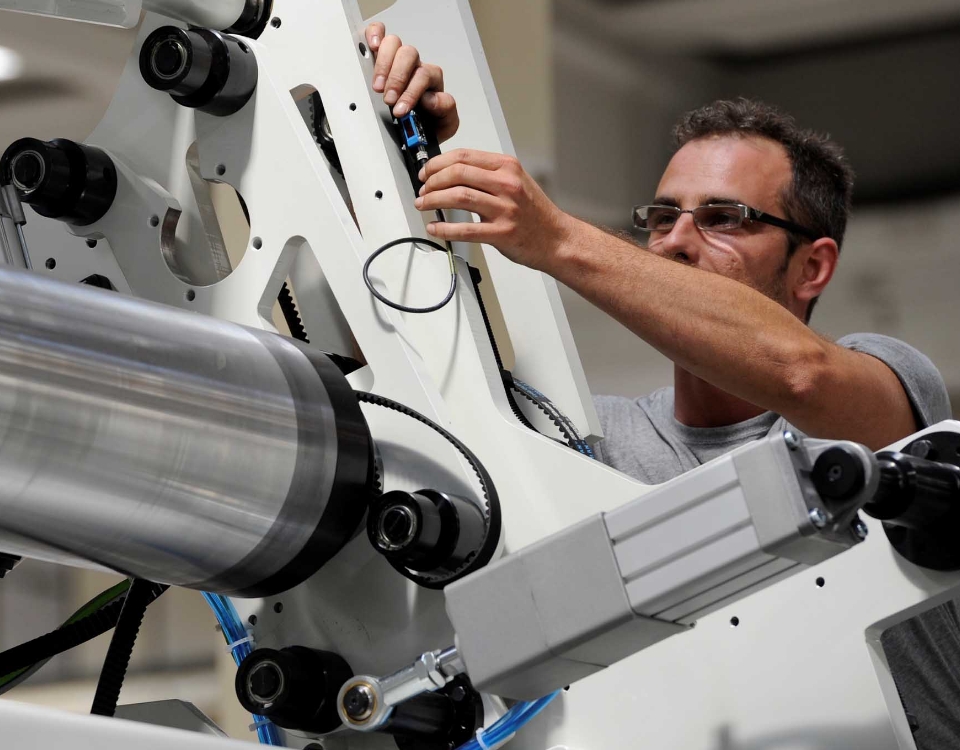
This folder also features:
- Stand-by energy-saving system
- 2 sliding front supports
- DSP-AP laser safety system with PLC
- 1 standard foot pedal
- Pneumatic bending table with 60 mm width
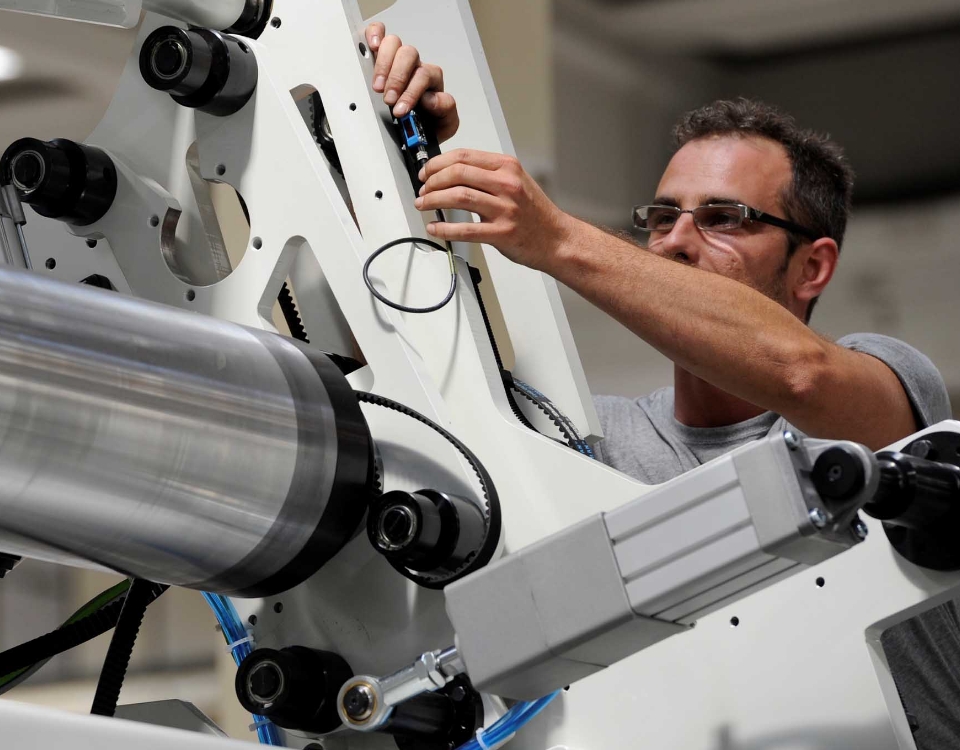
X-Press 30/1250
The second press brake with Design Next has n open-height of 400 mm and the Y-axis stroke is 200 mm. The machine features the E-Reflex deformation compensation system.
X-Press 30/1250
The machine is equipped with the same DSP-AP safety system as the first one.
The customer chose to equip the press brake with the Delem DA-66T CNC mounted on a top-hanging arm and the Delem Profile Lite TL 2D offline software, which ensure ease of use and state-of-the-art technology. The touch screen provides access to the proven user interface and direct navigation between programming and production.
In addition, communication standards compliant with Industry 4.0 Intelligent Factory models have been installed.
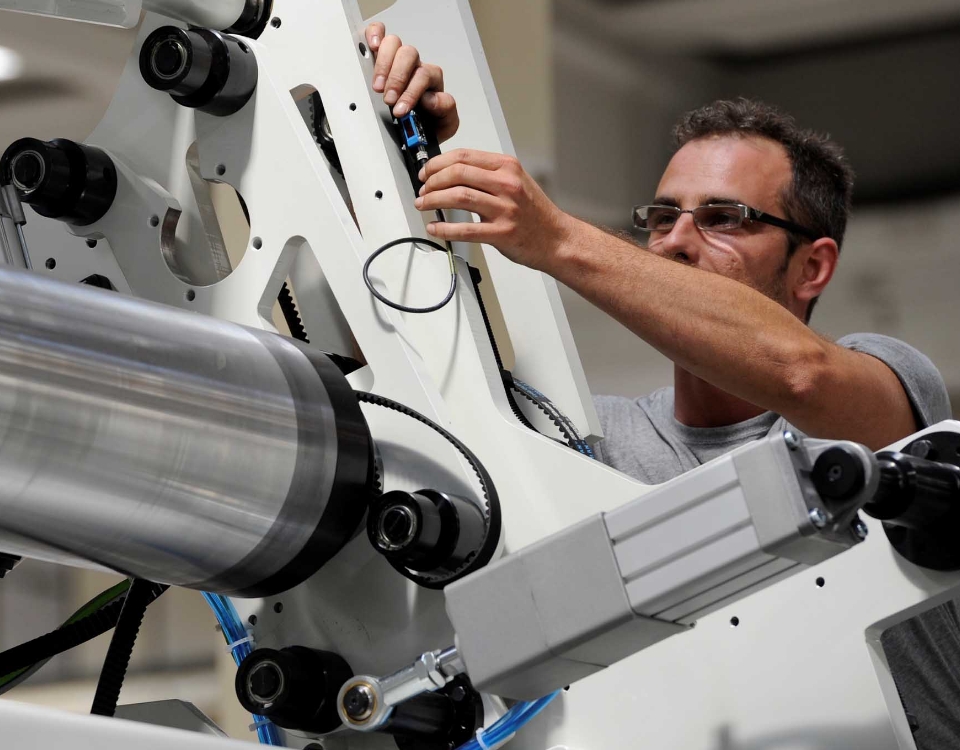
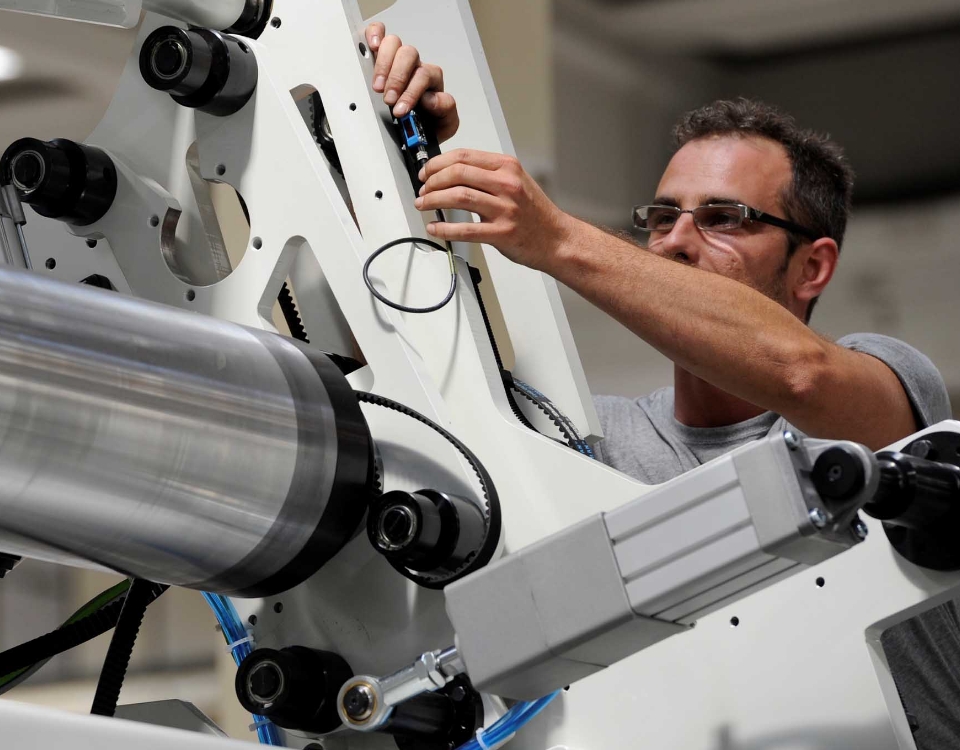
X-Press 30/1250
It has manual ram clamping and manual lower clamping.
The backgauge is 4-axis (X-R-Z1-Z2) CNC-controlled, with an additional stop on a reference.
It has also been equipped with:
- height-adjustable foot pedal device
- LED lighting of the work area
- tool cabinet
- ergonomics kit