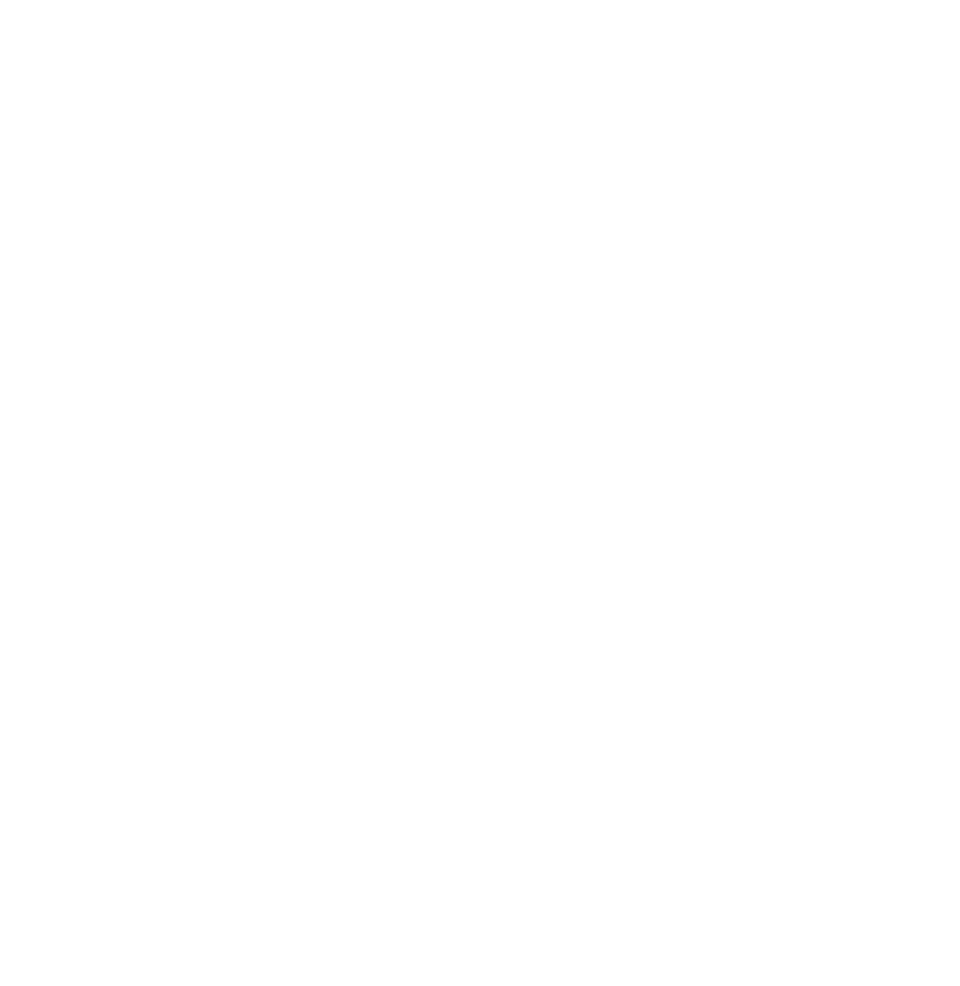
Tandem press brake: how it works and what are the advantages
This press brake is designed to be placed side by side with another 1000 ton / 7000 mm machine, which Compagnia Siderurgica already has at its disposal.
In this way the two presses can work individually or in combination.
The main technical features of the press brake
This press brake is equipped with Gasparini Adaptive Crowning system: to adapt in real time to the ram deformation, Gasparini relies on two precision sensors. The first one detects the ram bowing since the start of the bend. The CNC activates the cylinders in the lower ram until the reading of the second sensor is equal to the first one. The CNC drives the pistons in the lower crossbeam until the measurement of the second sensor is equal to that of the first. In this way, the two cross beams are perfectly parallel. The result is total control of the angle, with maximum precision and absolute repeatability, with all materials.
The choice of safety system
This press brake is equipped with the Iris Plus laser safety system with PLC.
This safety system uses a two-dimensional die sensor to read the entire area around the punch tip.
With an optical resolution of only 2 mm, it allows the speed change point to be set at 0 mm from the sheet. The cycle time is greatly reduced: up to 3 seconds saved per bend. The maximum distance between the systems is 15 m.
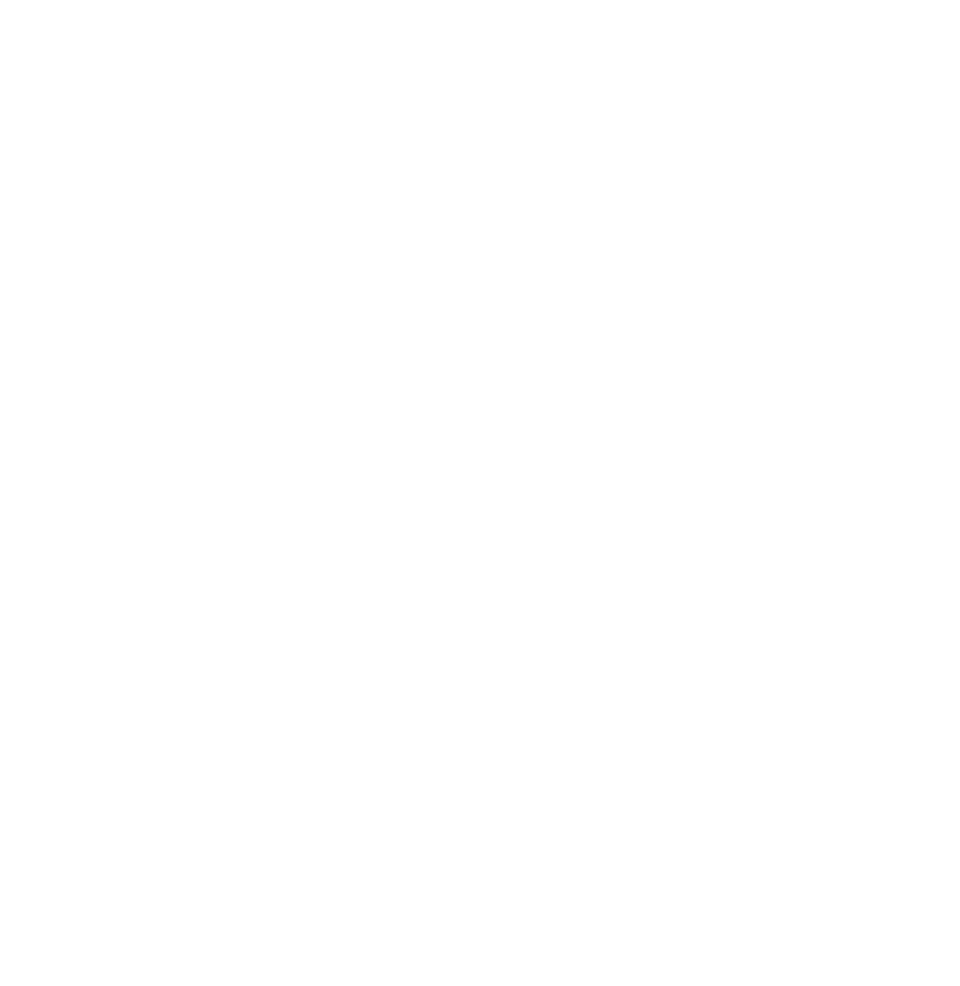
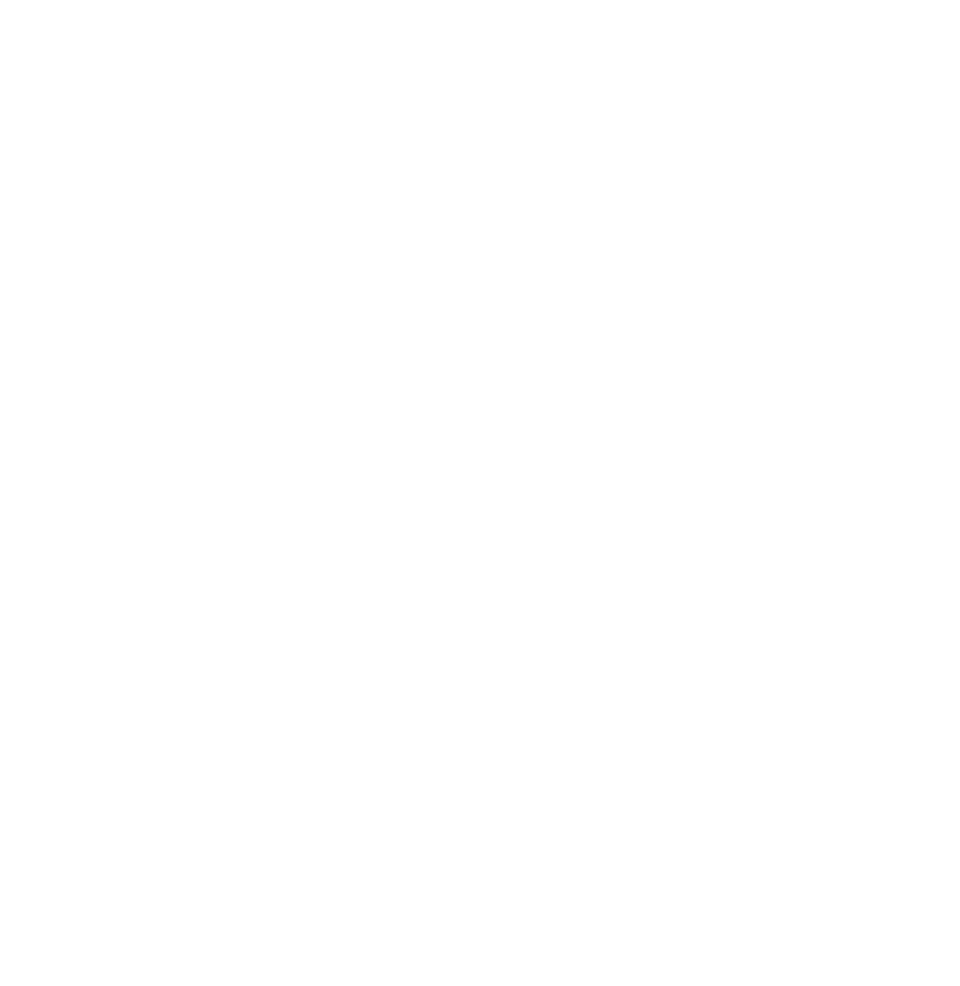
Ram protection
To overcome the problem of parts of a certain size/size colliding with the upper ram, protective strips have been applied to the ram. In this way, longer metal sheets or special boxes do not collide directly with it and the machine remains protected from scratches and other resulting damage.
The choice of clamping system
The upper clamping system is hydraulic self-aligning type H-GG for punches or tool adapter (hardened plate on upper ram).
The lower clamping system is also hydraulic.
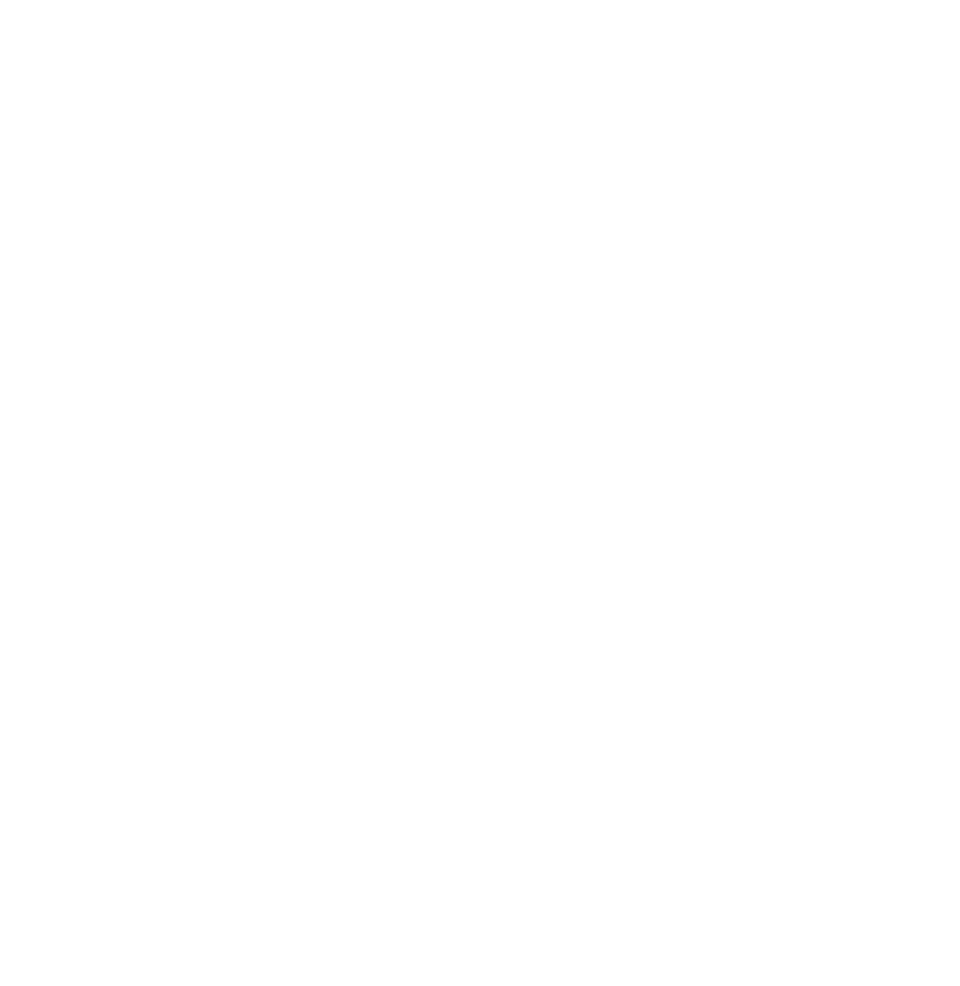
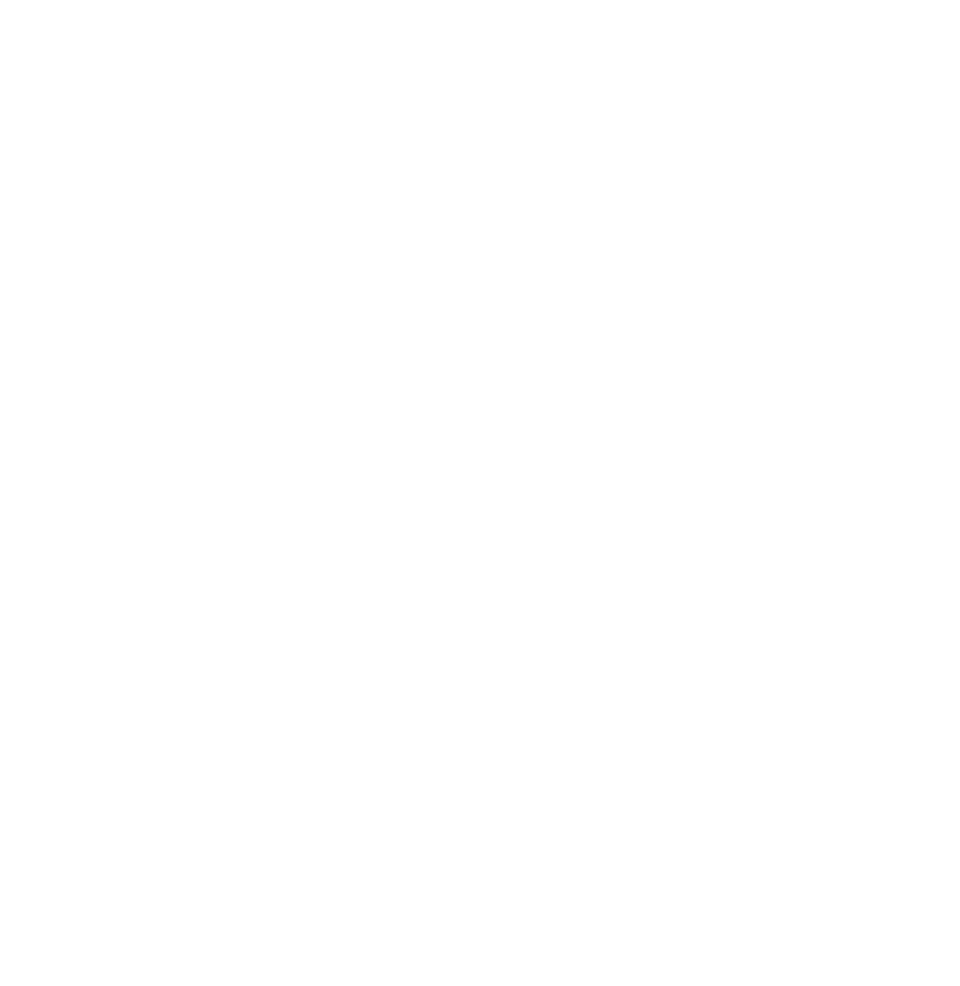
How to achieve more precision and ergonomics when bending sheet metal
The backgauge has 4 axes (X-R-Z1-Z2) controlled by CNC, and an additional reference has been added.
The CNC is the Delem DA-66T, equipped with DM10x modules (for uniformity with the existing machine), and is mounted on a mobile pulpit. The offline software is Delem Profile Lite TL 2D.
The machine has two standard foot pedals.
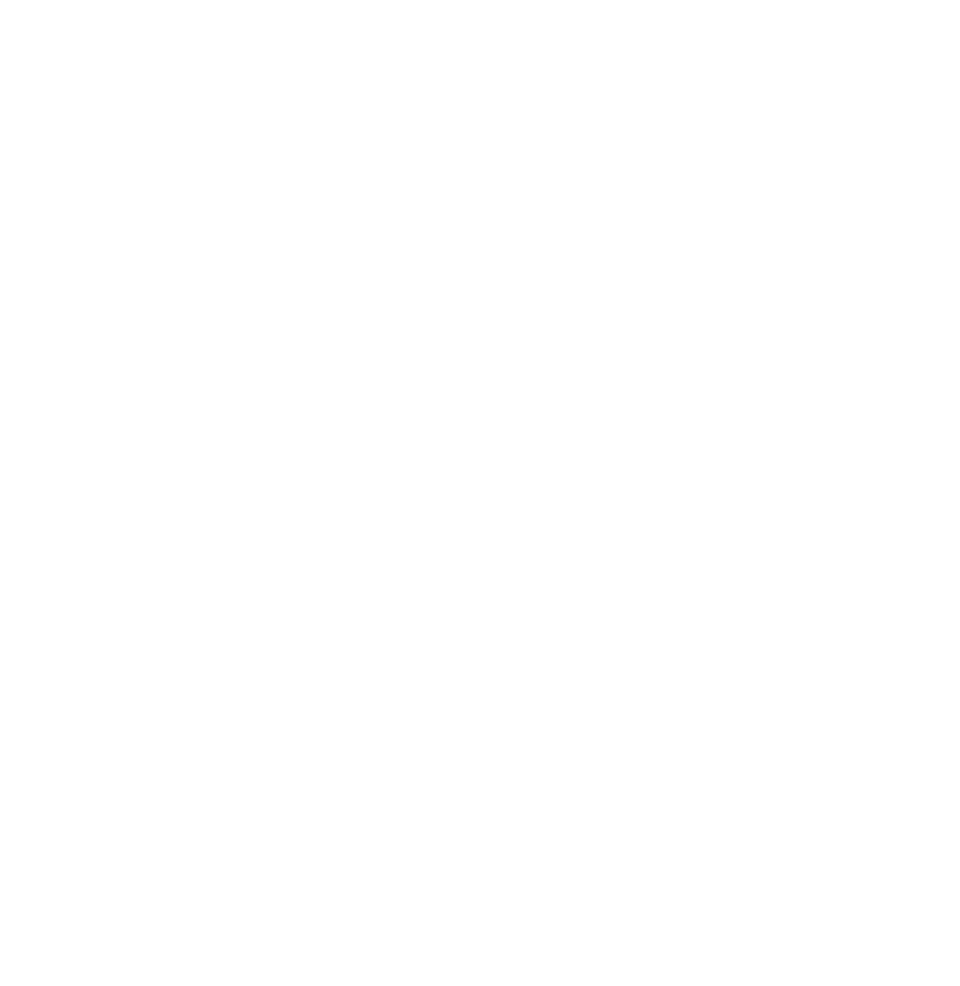
Additional accessories and customisations requested by Compagnia Siderurgica
Compagnia Siderurgica has chosen to set up the press brake for Tele-Link remote assistance and install the Industry 4.0 package.
In addition, this press brake features:
- Stand-by energy-saving system
- 2 standard front supports
- LED lighting of the working area
- Electrical and CNC cabinet on the left side
“After more than 30 years of experience using Gasparini machines, we can certainly affirm the high quality of the product and the excellent after-sales service, always prompt and effective.”